Connected Automation: The Concept
Connected Automation is an approach to maximizing customer productivity, using KP-Connect Pro to centrally connect production systems and machines equipped with labor and work saving technology.
We provide unique, open environments for joint development with a variety of manufacturers and vendors around the world.
Achieving Connected Automation with Komori Products
Connected Automation is Komori's concept for creating Smart Factory.
Connected Automation is Komori's concept for creating Smart Factory by promoting use of IoT (the Internet of Things), developing labor and work saving designs, and strengthening standardization and inspection mechanisms. Through products such as KP-Connect, offset presses, digital presses and PESP postpress solutions, Connected Automation helps improve customer productivity through machines equipped with labor and work saving technology, and through connection of manufacturing workflows.
KP-Connect, Komori's IoT cloud service for visualization of data, continues to evolve as the printing industry changes. With a single click KP-Connect can aggregate operating status data on a job-by-job, weekly or monthly basis. Detailed breakdowns of schedules and improvements are available to better increase efficiency, including changeover times, registration/color adjustment times, final printing times and idle times included in jobs. KP-Connect Pro, an ugraded version for process management, saves work and labor for overall production processes by linking and coordinating not only printing presses, but also MIS, prepress, press and postpress devices. As part of support efforts, Komori has also begun offering a service whereby we collect data from participating customers to issue daily and monthly reports.
Our offset presses offer Parallel Makeready, a design concept focused around creating systems that carry out print preparation tasks simultaneously, so as to minimize the time used by machines. We are also aggressively pursuing development of products geared toward increased automation, such as with our Autopilot concept, which focuses on creating systems that use automation technology to assist in tasks for which human judgment is still required.
In addition to the Impremia IS29, our digital press lineup includes the new Impremia NS40 (40'' Sheetfed Nanographic Printing® System) model, which can be used like an offset press and offers maximum printing speeds of 6,500 sph at B1 size.
In postpress solutions we offer the Apressia CTX (programmable hydraulic clamp cutting system), which handles cutting processes in a systematic manner to save work and labor. We are also pursuing development of automation solutions, for final inspections, that involve use of all-4K cameras for highly accurate inspection of blanks.
Through Connected Automation, Komori is fully committed to supporting increased productivity in the printing industry through development of all elements necessary for Smart Factory printing.

About Smart Factory -- Komori's Approach to Increasing Productivity
What does a Smart Factory look like, in the printing industry?
And what can companies do to save work and labor, and maximize productivity?
Key areas to focus on include use of IoT (the Internet of Things), development of labor and work saving designs, and strengthening of standardization and inspection mechanisms.
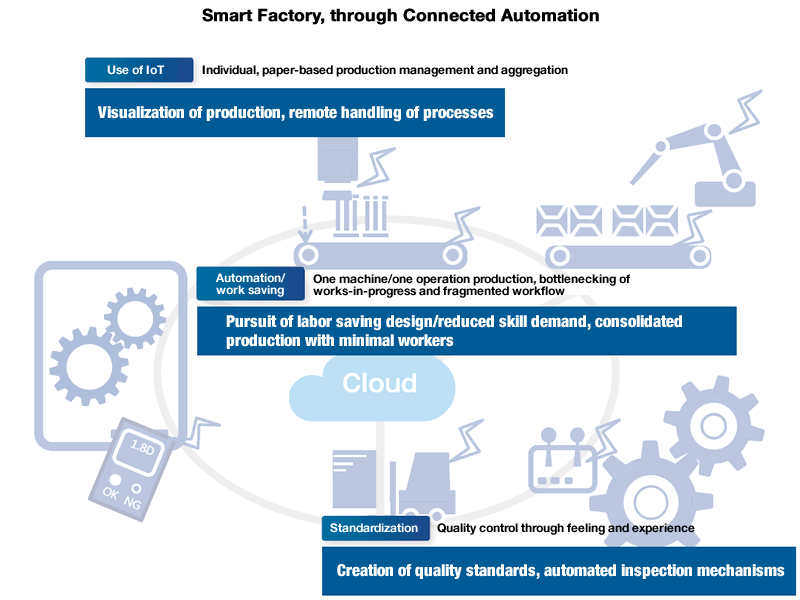
Use of IoT (Internet of Things)
The data collection→storage→analysis→application cycle forms the basis of a Smart Factory.
Through this cycle, plant data is visualized and analyzed, clarifying areas that are in need of standardization and mechanical solutions in order to remove bottlenecks and streamline processes plant-wide. Once a plant begins to implement these solutionsand transforms into a Smart Factory, labor and work saving results will also be seen for machine operations handled by workers.
Currently MIS has been introduced for a significant number of printing plants, but most only use it for order processing and accounting. Application of MIS to production process management and calculation of base prices is still lagging.
MIS must be used more strategically. In addition to linking start and finish data for each process via network, more detailed machine operating data (such as preparation times, operating times, number of waste paper sheets and start-up printing counts) can be collected on a per-job basis, eliminating the need for daily operator reports and allowing weekly and monthly results to be analyzed from a variety of angles.
For instance, identifying bottlenecks that occur between processes can allow for more accurate assessment of price controls (i.e. manufacturing hours spent) per job.
Furthermore, if the network is internet-enabled,operating data can be checked at any time via mobile, allowing sales people to check job progress even while out of the office.
By connecting machines to MIS, information such as job names, paper details (thickness, size, type, etc.), run size and number of finished copies can be communicated to each process without needing to be re-entered, reducing the hassle of entry as well as the risk of mistakes.
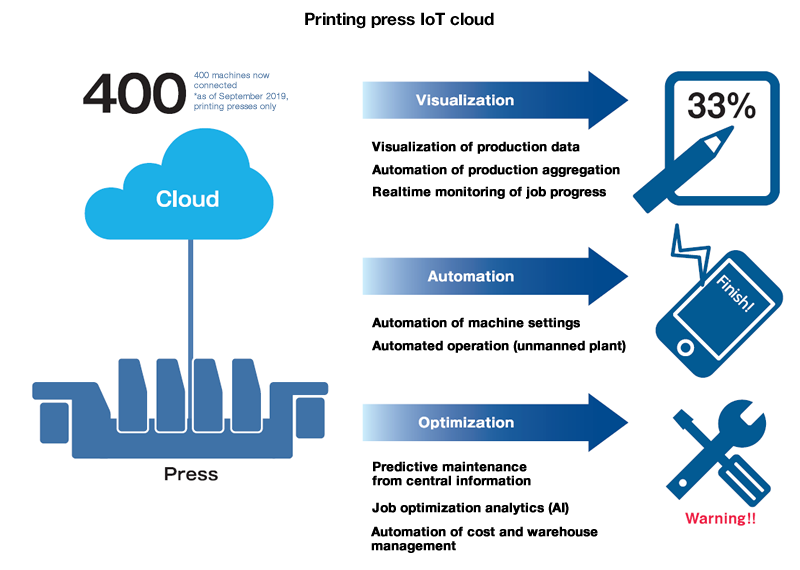
Labor and Work Saving Designs
Labor and work saving technologies for prepress processes have evolved in recent years, bringing significant changes. With the introduction of DTP and CTP, the creation of printing plates, which used to involve large numbers of skilled workers toiling in darkrooms, has been completely revolutionized. In printing processes, new automation systems have been introduced for steps such as press cleaning and changing of plates.
New print quality control devices are also being introduced that use equipment such as cameras and scanners. However, production and postpress processes continue to be handled largely by hand.
In postpress, although many finishing processes involve simple and repetitive actions, they still require large numbers of workers, which hinders productivity. Furthermore, as these processes are the final steps before shipping, delivery can often be tight, sometimes forcing departments to throw their entire workforce at the problem in order to meet deadlines.
Time management is integral to saving work and labor during these processes. Printing companies need to grasp the numbers of workers and amount of time they are spending on current tasks, and calculate how efficiency can be improved through steps such as introduction of new equipment and improvements to workflow. Efficiency can be improved by introducing unmanned operation, labor-saving designs and then work saving designs (eliminating the need for special skills), in that order.Re-evaluating postpress productivity can create labor surpluses that can further improve plant productivity.
Strengthening of Standardization and Inspection Mechanisms
When analyzing visualized data and introducing labor and work saving designs, it is essential that quality management be preserved. The level of print quality management in Japan is among the most stringent in the world, and is supported by highly experienced technicians. However, the number of veteran print operators is dwindling, as is the number of clients with in-depth knowledge in printing. In order to achieve a Smart Factory while maintaining the same levels of quality, it is absolutely vital that processes be standardized so that the same end-product can be achieved, every time, regardless of the operator.
For instance, while the majority of presses are currently equipped with colorimeters, it appears that in many cases they are not being used correctly. One of the leading causes of this is related to proofing. When proofing is done by hand and pages printed under differing conditions are pasted together, standardization becomes difficult to achieve. The first step is to standardize proofing methods.
In recent years it has become popular to use inkjet printers for proofing, because of the ease of color management. If proofing quality were standardized, however, printing would likewise become easier to standardize. In fact, the majority of work can be standardized and sped up, through use of CTP for highly accurate plate creation, and use of press color compensation features in conjunction with CIP4 data.
Additionally, there are a number of features that use tools such as colorimeters and cameras to monitor, control and record quality, even after final printing begins, and these features are steadily growing in popularity. Cameras equipped on presses and bookbinding machines for inspection of individual sheets have grown more accurate, offering better quality control. Additionally, equipment has recently become available to ensure traceability for defective and removed sheets, such as devices that create PDF images from platemaking data for comparison with printed items, or numbering systems that use inkjets to print a unique number on every sheet. Adopting the best equipment currently available allows printers to reduce the number of inspectors and better visualize quality, while still maintaining the same quality standards.
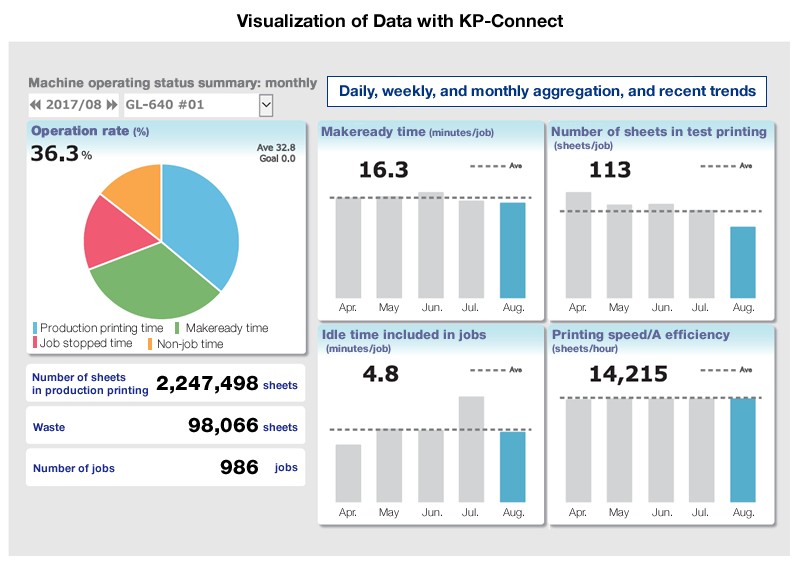
