Propelling new business with the highest operating rate of 49.4%
Japan, Smart Graphics Co.,Ltd | Lithrone G37P [GL-837P] / KP-Connect
14 October 2020
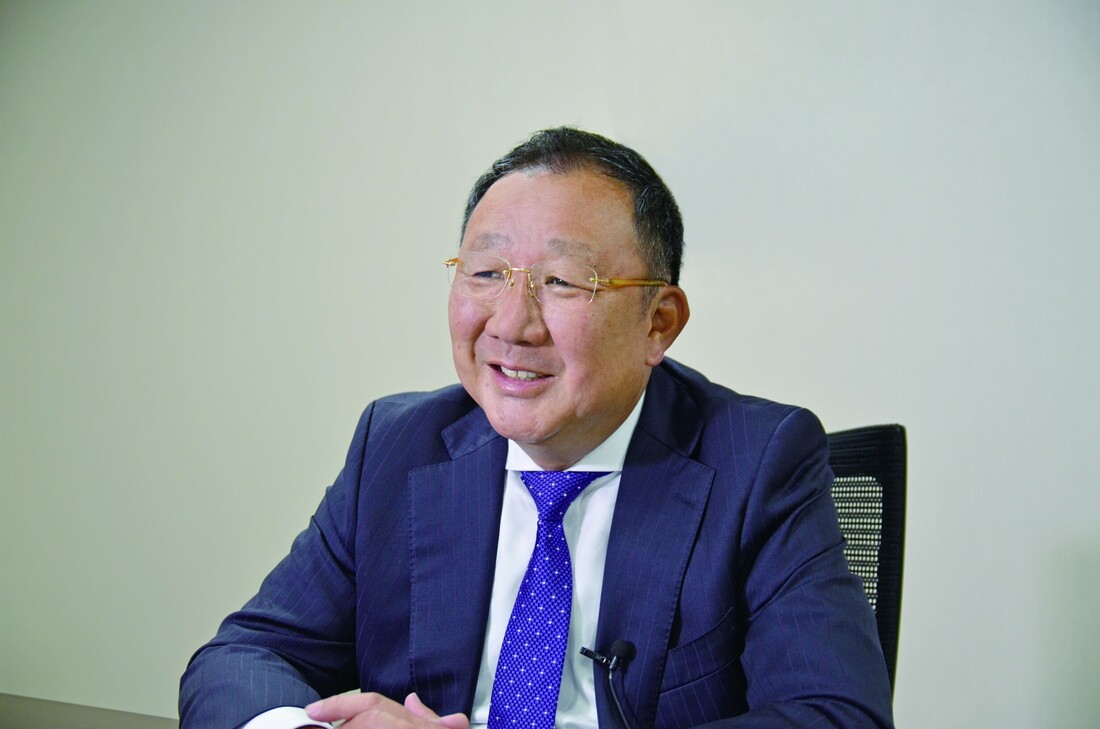
"The newly introduced Lithrone G37P and KP-Connect are contributing greatly to our new business."
Hiroshi Fukuda, President and CEO
Smart Graphics interview video
Uematsu Co., Ltd is pursuing a business model as a printing company foundry (dedicated outsourcing manufacturing company) specializing in the manufacturing sector and with this new model the company continues to grow. Smart Graphics, strategically positioned in the Uematsu Group to tackle new business. The Lithrone G37P with a LED UV system was introduced as the main press for this new business model. The press was installed at their new plant that began full operation in October 2019.
Selected themes for the printing press: "Conserving Materials" and "Saving Time"
President Fukuda says that the new plant will achieve their goal of a "smart factory".Four printing presses were installed in the new plant. Of those, three are new presses.
"While we have always been chasing greater productivity, there are barriers that we cannot overcome. How quickly we can perform color matching on the proof is essential to increasing productivity. Up until now, we have attempted to always maintain a unified sheet concentration using color management and a colorimeter, and match with digital proofs, which have increased in amount. In the new business we are printing efficiently without a proof and we now have achieved consistent quality with Japan Color standards. The key to small-lot printing is to produce a greater number of jobs that can be printed at the same level of quality and stable color without spending much time on color matching. Furthermore, we decided to adopt the LED UV system in order to reduce the amount of time spent on post-processes."
Thus, they chose the Lithrone G37P with a LED UV.
"There were two selection themes. One was conserving materials and the other was saving time. In terms of conserving materials, the large plate size of the Lithrone G37P is an extremely efficient plate size that is capable of printing sheets up to A1 in size, and can also conserve blankets and other materials. Regarding the time saving, we were drawn to Komori's "Parallel Makeready" which speeds up the makeready time so we can spend more time printing. Parallel Makeready performs three tasks simultaneously: blanket washing, plate changing, and pre-inking."
Visualization with KP-Connect: Highest operating rate of 49.4% in a single day
The KP-Connect screen that shows the operating rate
It has been six months since the Lithrone G37P started operations. President Fukuda states, "We have achieved a productivity of four times that of conventional printing presses."
As a result of focusing most on return on investment (ROI) when we considered a printing press, we decided to introduce the Lithrone G37P, and the benefit of KP-Connect together which resulted in our high operating rate. Director Fukuda says the following about the use of KP-Connect.
"With the introduction of KP-Connect, the three things we focus on are the operating rate, start-up time, and the number of test sheets. As we are specialized for manufacturing products for the printing industry, we cannot control unit costs. In order to increase gross profit, we need to reduce start-up time and waste. Normally, start-up takes about 10 minutes, but we have reached times as fast as six minutes. This is a quarter of the time taken in the past. If we can improve operator proficiency, we can achieve a time of six minutes consistently. The number of test prints and makeready time are both decreasing." He continued by saying that they are seeing outstanding figures for operating rate. "The operating rate is as high as 49.4% on a single day. Of course this varies depending on the size of the lot, but the average figure is very high compared to other presses."
Director Kaneko, who oversees production management, said, "The Lithrone G37P presses are all fully automated. All the operator has to do is perform maintenance and run the press at full speed, and compared to our existing machines, it has greater visualization due to the KP-Connect data with job status information."
From left: Keisuke Fukuda, Planning Director, Jun Kaneko, Production Control Director
Striving for integration including automation of in-plant transport and post-process
In regard to Parallel Makeready, Director Shimizu said, "The press is ready for final printing in a flash. In order to launch the new business, the reduction in preparation time and stability was most important. As the register and color matching is almost perfect, we can do a final printing after two test runs."
But the pursuit of greater productivity at the new plant isn't completed. President Fukuda says, "We are aiming for an operating rate of over 50% and we are planning on purchasing another press. In the future, we will also aim to create a comprehensive "smart factory" by automating transportation in the plant and connecting the guillotine and folder as one system."
Toshihiro Shimizu, Production Director