Direction of Decarbonization in the Packaging Industry
27 October 2021
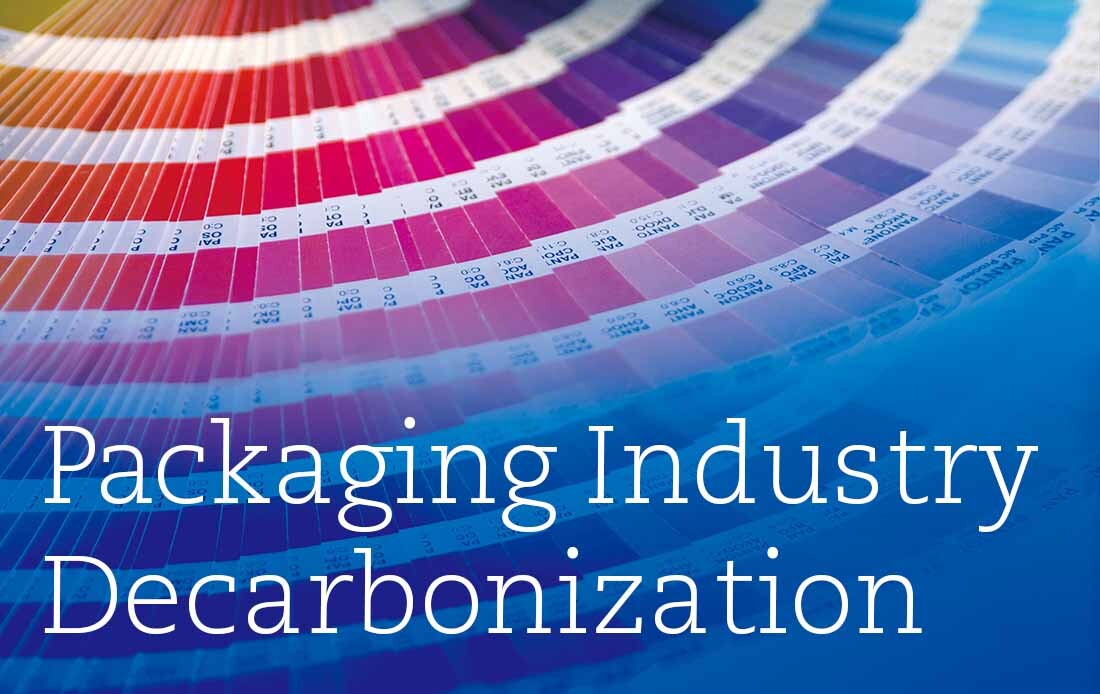
Movement toward a decarbonized society is gaining speed around the world. Most companies have responded to this movement and declared decarbonization and a commitment to carbon neutrality as one measure in their transformation and growth strategy. The printing industry is also feeling the effects of this general trend. For example, industry-leading brand owners in sectors such as daily necessities, foods, cosmetics, and pharmaceuticals have begun moving to adapt. To achieve their own decarbonization goals, they are asking stakeholders, including package printing companies, to cooperate and respond to their demands to reduce CO2 emissions. For the printing industry, decarbonization is already a familiar topic. Although decarbonization is a serious matter that must be addressed, many are concerned that environmental measures will impose extra costs. Is this true?
Will decarbonization increase costs?
Up to now, environmental measures and improved profits have been considered contradictory. However, recent analysis has shown a different picture. As a specific example, we will explain the relationship between labor productivity and carbon productivity. [Figure 1]
From Ministry of Health, Labour and Welfare "2016 Analysis of Labor Economy" (summary)
In this figure, the horizontal axis shows labor productivity, and the vertical axis indicates carbon productivity per ton of CO2 emissions. First, we can see a positive correlation between countries with high labor productivity and high carbon productivity. Switzerland, Sweden, and Germany are likely to have high labor productivity and high carbon productivity. This means they tend to reduce their CO2 emissions while being highly productive and profitable. Many countries have already made progress in both productivity and decarbonization.
Now, let's look at the relationship between carbon productivity and return on assets (ROA) by industry. [Figure 2] This figure shows carbon productivity (horizontal axis) and ROA (vertical axis) in Japan. The transportation machinery and equipment manufacturing industry, which includes car makers, as well as the metal products manufacturing industry generate profits more efficiently than other industries and tend to have higher carbon productivity. Unfortunately, the pulp, paper, and paper products manufacturing industry, which is related to printing, at present has a low ROA and low carbon productivity. On the other hand, there is more upside potential than in other industries.
Opinion exchange forum with the younger generation regarding "long-term strategy as a growth strategy based on the Paris Accord" held on May 14, 2019 (tentative) (draft)
Decarbonization as the growth strategy; from materials of Professor Toru Morotomi, Kyoto University Graduate School of Global Environmental Studies/Kyoto University Graduate School of Economics
From these examples, we can see that by increasing productivity and eliminating waste, it is possible to increase profits and decarbonize at the same time. Therefore, the printing industry appears able to achieve both increased profits and decarbonization.
This article focuses on three areas of the packaging industry: the printing process, the printing plant, and supply chain transformation in printing. Solutions are proposed for productivity improvement, that is, decarbonization, in each area.
What is productivity improvement in the printing process?
First, we will focus on the productivity of the printing process. In the printing industry, the demand for small-volume production and quick delivery is increasing. To increase productivity, presses that focus on higher printing speeds and shorter makeready times have the highest return on investment (ROI).
The Komori Lithrone GX/G advance series presses deliver world class ROI. Improvements to the high-speed stability of the feeder, delivery, and Komorimatic dampening system have enabled stable, high-speed printing. The operating system has also been updated, and operator touchpoints have been significantly reduced. In addition, automatic job presetting in coordination with KP-Connect Pro dramatically reduces makeready time. With these improvements, the Lithrone GX/G advance series presses achieve critical productivity goals. [Figure 3]
This overall increase in productivity allows 'downsizing,' the consolidation of older technology into the latest technology with high production efficiency. For example, by consolidating three old presses with low productivity into two new presses with high productivity, greater production volumes can be achieved while significantly reducing paper waste and power consumption, resulting in higher profits and a major reduction in CO2 emissions. [Figure 4]
This kind of downsizing can only be realized with the performance of the Lithrone GX/G advance series presses, which have greatly improved productivity.
Turning the entire printing plant into a Smart Factory
There are many processes at the printing site, and with analog process management using job tickets and telephone calls, coordinating before and after processes and responding to changes in conditions is difficult, so there is a limit to raising overall productivity. In other words, to improve productivity on the printing floor, optimizing the entire process is more important than improving the productivity of individual processes. Innovation through Digital Transformation (DX) of the entire production process is the key to solving this problem.
Komori's Connected Automation concept turns printing plants into Smart Factories by connecting the entire printing process, which is fragmented into individual processes, using digital technology. KP-Connect Pro is the middleware that forms the core of this concept.
Based on an open platform concept, KP-Connect Pro is currently being connected to many manufacturers and vendors. Printing companies can then combine and connect not only new devices but also existing devices. When each process is connected digitally, the entire process can be visualized and optimized. Real-time information on operation enables bottlenecks to be identified and immediate action to be taken. This not only prevents losses but also leads to increased profits.
KP-Connect Pro has already been installed in printing companies both in Japan and overseas, and in many cases it has significantly improved productivity and profitability. Komori believes that the digital transformation of the entire production process is already a real prospect and that its effects will be extremely significant.
KP-Connect Pro has become a more practical system because its functions have evolved in response to the opinions of customers. In pursuit of the ideal form of digitalization of the printing process, we continue to make progress.
As noted, Komori believes that if the productivity of the printing plant is improved, energy efficiency will be increased, which in turn will reduce CO2 emissions, thereby contributing to a decarbonized society.
KP-Connect Pro will greatly contribute to the transformation of printing plants into Smart Factories.
Supply chain transformation in the printing industry
One of the greatest challenges in package printing is the use of special colors. The makeready cost for color changeover and roller cleaning with special colors can be very high. Printing companies often must produce in large lots to meet budgets, and, for example, producing six months' worth of products that are to be delivered once a month. However, if there is a change in the design midway, the inventory must be scrapped, resulting in a loss, which further drives up costs.
Minimizing makeready costs and implementing a production system that is profitable for small quantity runs is ideal. If printers can produce in small lots and deliver on a just-in-time basis, there will be no need to hold inventory, and inventory risk can be eliminated, and costs reduced drastically. This is Komori's concept of supply chain transformation in the printing industry. [Figure 5]
Komori can provide two solutions for supply chain transformation. One is Smart Color, a technology that simulates the reproduction of special colors, and the other is the Impremia NS40 digital printing system.
Smart Color reproduces a wide gamut of special colors using seven colors -- CMYK+O (orange), G (green), and V (violet). Seven colors can reproduce 88% of the Pantone color palette (*1), and six colors can reproduce 80% of the Pantone color palette.
Fixing the ink types eliminates the need for color changes and roller cleaning, and the ability to numerically control colors dramatically reduces makeready time. When equipped with parallel control of advanced functions, plate changing, blanket washing, and pre-inking can be performed simultaneously, enabling more efficient changeover. [Figure 6]
Although the idea of process color production of special colors has been around for a long time, it was thought difficult to implement in practice because it could not accurately and stably reproduce colors.
To express a variety of special colors using a combination of dots, the printing press must have high-precision dot shape reproduction and highly stable water film control. Komorimatic uses a unique configuration of four dampening rollers and a reverse-slip system to form a uniform water film thickness in both the lateral and vertical directions, minimizing unevenness. The accuracy of the Komorimatic dampening system and the ink keys and the film thickness control system that precisely form the ink film thickness enable process reproduction of special colors within ⊿E3. This technology leads to realizing Smart Color. [Figure 7]
* The effects of installation and improvement described herein have been estimated and measured under fixed conditions for the purpose of providing information for reference in making investment decisions and are not a guarantee of actual effects.
For ultra-small-lot package printing, the Impremia NS40 digital printing system offers the ultimate in makeready cost reduction.
The Impremia NS40 is a digital printing system that enables ultra-small-lot printing and quick turnaround on B1 stock and delivers a printing speed of 6,500 sph. In addition to the features of digital printing that minimize the makeready process, the Impremia NS40 can reproduce 96% (*1) of Pantone's special color palette using seven colors, making it the digital packaging printing machine for the future. It is capable of printing small lot jobs on demand, enabling operation without holding product inventory and without waste loss.
The direction of decarbonization in the packaging industry
In April 2021, the Japanese government announced an ambitious greenhouse gas reduction target of 46% by 2030 (compared to fiscal 2013) amid growing awareness of environmental issues worldwide, accelerating the movement toward decarbonization of society. The printing industry, especially the package printing industry, is expected to be greatly affected by this. To achieve this goal in less than ten years from now, it is imperative to start decarbonization efforts now, and companies that fail to respond may face harsh criticism from brand owners and end-product consumers.
As mentioned above, the key to the solution is maximizing productivity and eliminating waste to improve profits and ultimately achieve decarbonization. There is no contradiction between business and decarbonization, and, in fact, it is thought to be driving enhanced competitiveness in some countries.
*1: Pantone coverage figures are current as of September 2021 and are subject to change without notice.