The Strategic Introduction of the Lithrone GX40RP advance Strengthens Full-fledged Integrated Production from Small to Large Lots
Japan, Kyodo Printing Media Product Co., Ltd. | Lithrone GX40RP advance [GLX-1040RP-A]
24 January 2023
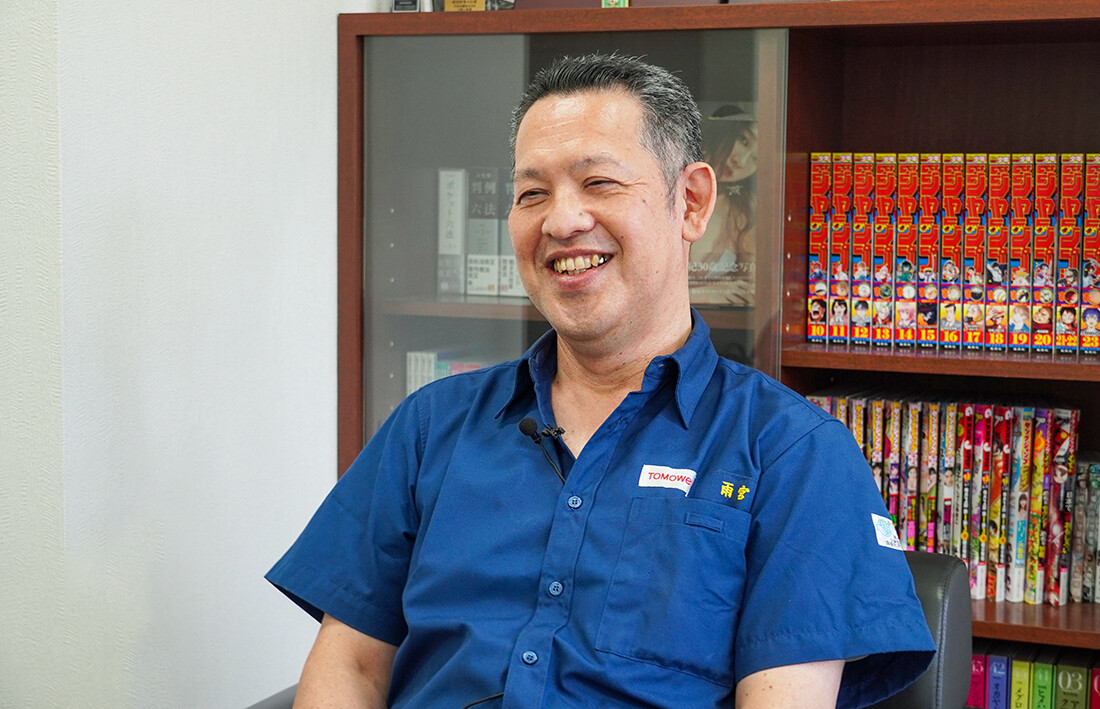
"I once more perceived what people should do when this degree of automation is achieved, and this leads to the discovery of points for further improvement. I'm really looking forward to making full use of the functions."
Hiroaki Amemiya, Director and Plant Manager
Goka Plant
"Reductions in paper, energy, and transportation naturally lead to reductions in CO2 emissions. This press not only greatly reduces waste paper but also contributes to integrated production. When printing can be completed this quickly, postpress processing must also be more efficient, and the challenges in ensuring even more efficient production become apparent."
-- Hiroaki Amemiya, Director and Plant Manager
The Goka Plant, the core of the Kyodo Printing Group's publishing and commercial printing business, was built in 1993, during the heyday of weekly comics magazines. The strength of this factory lies in its production system, which allows platemaking, printing, processing, and delivery to be completed in one location. In May 2022, the plant installed the Lithrone GX40RP advance (40-inch double-sided offset printing press) to further strengthen integrated production. We asked Hiroaki Amemiya, Director and Plant Manager of the Goka Plant; Takao Nagai, General Manager, First Manufacturing Department; and Hideki Iwano, Section Manager of the First Section, First Manufacturing Department, about the installation process, the assessment after operation, and the outlook for the future.
RP press is the essential choice due to work flexibility
About 400 people, including those from partner companies, work at the Goka Plant on a site of about 80,000 square meters. The plant manufactures a wide variety of publications and commercial printed materials, providing one-stop services ranging from printing to bookbinding, wrapping for individual shipments, sorting, and shipping.
Regarding the concept of equipment supporting the plant's integrated production system, Plant Manager Amemiya said, "From a profit, cost, and productivity standpoint, a one-pass double-sided press is essential. Since the customer's paper is used for nearly all our publication printing, a press with paper-size flexibility is required. A perfecting press was not an option due to the margin at sheet tail, so we chose the RP press, which offers a single-sided gripper configuration with no limitations on paper size."
This time, the decisive factors for choosing the Komori press were the applicability to current production and the possibility of handling high-mix, low-volume printing. "The RP press is superior in terms of maximum printing speed and paper loading capacity, and we judged that it would be sufficient for production for current business. For small lot production, which is increasingly accelerating, a press and equipment offering quick changeovers were necessary. It is just shortly after the press's introduction, even though the average lot size is one half and job changeovers are about twice as many compared to our existing double-sided UV press. High operating results have been obtained and output is more than equal although it is an oil-based press. As to the number of colors, we adopted a press with six colors on the front side and four colors on the back side because we can print the front cover, which often uses special colors, and text in one pass," he explained.
Challenging automatic printing with parallel control
Speedometer indicates 18,000 sheets per hour. Realization of high-speed printing.
"For extremely small lots such as 1,000 or 2,000 sheets, we take advantage of quick changeover and finish printing right away. For large lots, productivity can be improved while maintaining quality by using high-speed printing and the color monitoring system."
--Takao Nagai, General Manager, First Manufacturing Department
"Since most of the work we do on the new press is small lots, we installed the latest printing system in order to print efficiently, quickly, and at low cost," says Nagai. "In particular, parallel control enables almost fully automatic operation from plate changing to start-up printing. In addition, jobs that require high quality are run on the RP press even for high-volume work due to its sharp reproduction of halftone dots." To handle high-speed oil-based double-sided printing, this press uses Komori's newly developed belt-type suction wheel in the delivery.
New belt-type suction wheel ensures stable sheet alignment and reduces scratches and smears.
"The new suction wheel has excellent paper braking and is quite effective in stabilizing paper alignment even at high speeds. The ability to preset not only paper size but also paper type is good," Nagai assesses.
Commitment to production with an emphasis on quality
The Goka Plant has positively implemented the use of quality inspection systems, and the RP press is equipped with PQA-S (Inline Print Quality Assessment System) and PDC-SX (Spectral Print Density Control System).
"We have changed from visual inspection to quality checks using the electronic eye, which is ideal," says Nagai. For color control in particular, "Target densities are obtained very quickly. Being able to check the current status on the large monitor from the start of printing is very desirable. Anyone can check the printing status of each color numerically, so that part of the operation is moving toward labor saving." Iwano said, "Color adjustments can now be made on the assumption that the operator does not touch the fountain keys."
Regarding the PDF Comparator System that can check the image information on the plate against that of the printed matter, Nagai gives his stamp of approval, saying, "This function allows the RP press to perform color measurement and quality confirmation at the same time." Amemiya said, "While there are many jobs with strict quality requirements, such as skin colors, we are getting high assessments from clients for quality, including color and register."
Young people bring dramatic changes to operator work
RP press operators
Regarding changes in work, Iwano said, "Due to the functions of the automated systems, press operation is no longer dependent on the experience and ability of the operator. Up to now, register adjustment for a double-sided press was time consuming for both front and back sides, and individual differences occurred. With the RP press, the method has completely changed because PDC-SX can automatically adjust register on both sides and it's possible to confirm numerically."
"This is a press with a concept on a completely different level than the presses we've seen so far. It's far exceeded my expectations."
--Hideki Iwano, Section Manager, First Section, First Manufacturing Department
"It's really amazing how the color matching can be done in the minimum number of times even for jobs with difficult quality requirements. My sense is that in many cases, it's at a level that's good enough to start production printing in the print start-up stage, and the number of test printings and sheets have decreased dramatically," he says. It also contributes significantly to the plant environment.
Nagai says that with the progress in automation, there has been a change in hiring. "It's actually easier for young people to learn how to use new functions. Since automation and numerical management compensate for the skills of experienced workers, we have selected a third-year employee to be the press chief."
"Honestly, the halftone dots are sharper than the proof sheet, which sometimes surprises me. I would like to advance standardization, such as adjusting platemaking, and deliver even better-quality printed matter."
--Takao Nagai, General Manager, First Manufacturing Department
The company is focusing on human resource development, and actively utilizes KGC's (Komori Graphic Technology Center) hierarchical operator training. The RP press operators are in training, and it seems that not only performance improvement on the system side but also these daily activities are the factors increasing the company's production efficiency.
Expecting further improvements in total strength
This new press is attracting attention even throughout the Kyodo Group and is positioned as a strategic machine that will lead to the securing of orders in cooperation with sales because of improved production efficiency.
"There are still many things I want Komori to do. I would like to ask for Komori's help in promoting further visualization, improving bottlenecks between processes, proposing preventive maintenance to reduce machine downtime, including for existing machines, providing more human resource training, and cultivating employees who can take on challenges such as the pursuit of what more can be done in printing," concludes Amemiya.