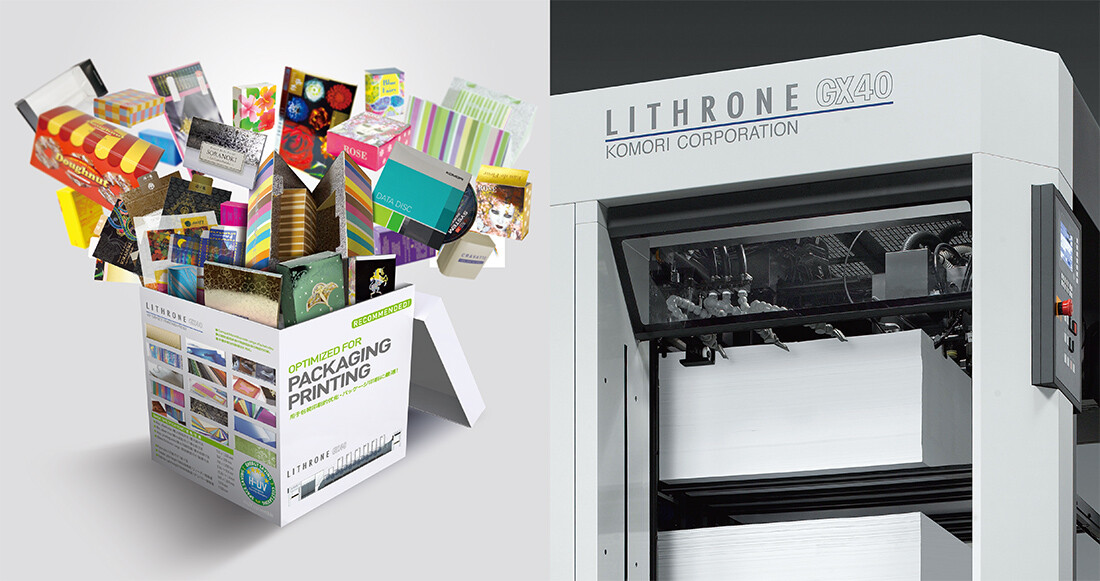
Nothing in the world of printing engages with every segment of the market and every moment of life like packaging. To consumers, a package is a seamless construct of varied materials in a range of colors that is trimmed with folds, caps, lids, labels, wrappers and other innovations aimed at ease of use. Brand owners, however, must keep a laser focus on every trend and variation in design and materials. Every shift in social values, regulatory frameworks and business models is reflected almost instantaneously in new packaging options. The design and development of packaging is a complex process of research, testing and surveys to create a form that generates consumer appeal and demand. Accurately reflecting shifts in demographics, lifestyles and tastes and providing choices of price, size and quantity are essential. Printers and converters must master the many particular processes and materials that go into packaging. And because packaging is unsurpassed in its capacity to reliably move products off store shelves, added value printing and finishing usually have an important place in the marketer's toolbox. In addition, each niche of the industry embodies so many unique characteristics that specialization is the rule rather than the exception.
Packaging must hold and protect, inform, express brand and product values, be sustainable, be biodegradable and meet a myriad of other subjective and objective demands. The need for unvarying accuracy and consistency means that a high degree of manufacturing expertise is essential. Distinctive applications and embellishments, special inks and coatings, and the full range of postpress processes are distinguishing features of packaging for the food, beverage, pharmaceuticals and cosmetics markets, which together account for about 75 percent of the packaging industry.
Finally, packaging is changing rapidly. Increasingly it is integrated into a marketing strategy that incorporates both the Web and social media. The use of nanomaterials in films and coating is opening up new performance potentials. And interactive and intelligent packaging using QR codes, RFID tags, 3D barcodes as well as printed electronics will eventually connect the package to the product in countless ways via the Internet, resulting in greater sustainability and new economic activity.
Komori is uniquely qualified to play a leading role in this segment of the printing industry for a number of reasons. For decades Komori commercial presses — both sheetfed and webfed — have been virtually synonymous with quality and robust engineering. Komori presses incorporate a level of automation found in no other machines. And many automated systems that are now nearly universal — like fully automatic plate changing — were developed by Komori. Software-driven digital systems that generate extraordinary efficiency are also fundamental to every Komori press.
The new flagship Lithrone GX40 sheetfed offset press for the most demanding applications, the distinctive Lithrone GX40RP with UV or H-UV, and the Komori-Chambon range of web presses. No one covers packaging like Komori.
Package Printing Open House at Tsukuba
On Thursday, June 12, 2014, Komori held its first Packaging Solutions Open House at the Tsukuba Plant, and this multinational, multilingual and multicultural event drew more than 59 packaging printers from some 17 countries to see Komori's products for the expanding package printing segment of the industry.
The event actually started the day before with a tour of the plants of nearby Komori users in the packaging business. On the day of the open house, visitors arrived at the Tsukuba facility just as a torrent of Japan's 'plum rains' was beating down.
Bullish outlook
Hans Hauben of Komori France delivered the morning presentation, starting with a review of the prospects of various segments of the industry and growth forecasts indicating the healthy outlook for package printing. Specifically, annual growth in OECD countries from 2012 to 2017 was forecast to be 2.10 percent while the growth in non-OECD countries was expected to be 8.10 percent.
Mr. Hauben outlined the current lineup of products for packaging and the Komori road map of product development for machines that will appear in the next few years, beginning with the offset, gravure and combined process web presses of Komori-Chambon. He also covered the Impremia lineup of digital printing systems, specifically the Impremia C80 toner-based system and the Impremia IS29 UV inkjet system (said to be "coming soon") as solutions for quick color matching and producing short runs of samples and packages.
The full-size Lithrones were then summarized — the Lithrone G40, the Lithrone S44, and the two machines that were to be demonstrated in the afternoon — the Lithrone GX40, available in a wide range of configurations with an extensive complement of optional systems, and the Lithrone GX40RP, the UV/H-UV-equipped 40-inch reverse printing press.
Demonstrations introduce new technologies
Following lunch, Doug Schardt of Komori America narrated the demonstrations of the six-color UV-equipped Lithrone GX40 with coater and the eight-color (4/4) H-UV-equipped Lithrone GX40RP. The fast print start-up, the quick matching of standard colors, the amazing performance of PDC-SX and PQA-S in tracking every imaginable variable, and the smooth pile changing of the nonstop feeder and delivery on the Lithrone GX40 guaranteed rapt attention.
Komori's flagship machine for fulfilling the most demanding requirements, this Lithrone was specified to exhibit precisely the characteristics required in a package printing machine: high maximum printing speed, unquestionable quality, nonstop operation, ergonomic engineering and end-to-end ease of use. The first job was 500 sheets of pharmaceuticals packaging run on 0.35 mm stock with medium ink coverage, and the second job was 2,000 sheets of confectionery boxes on 0.45 mm stock with heavy coverage. Komori showed how its automation has advanced, taking tedious tasks out of the hands of the operator and even extending its compass to postpress and bindery processes. Specifically, the demo emphasized that while KHS-AI is often thought of as an inking program that also handles air and register presets, the AI functions have grown exponentially over the years because of its higher level of integration with other systems. PDC-SX, PQA-S, PQC and the high-tech press itself are all Komori built, enabling a much richer flow of data for KHS-AI and other systems to work with than would be possible with separately sourced discrete systems. The robust Lithrone GX40 — complemented by the full range of Komori peripherals — will be a standout presence in the packaging industry for years to come.
Two jobs were run at the 16,500 sph maximum printing speed on the Lithrone GX40RP, laying down two colors on the back side and four on the front for both runs. The advantages of one-pass, two-sided printing without flipping the sheets as in a perfector were made clear as well as the fact that the direction of plate imaging is the same as for a straight press. Since no tail gripper is used to reverse sheets, there is no need for a tail-edge margin, meaning considerable stock savings. The same range of mechatronics options available for the Lithrone GX40 — including A-APC to change all plates in 85 seconds regardless of the number of units — may be specified for the Lithrone GX40RP.
Report from the front
All of the visitors then once again assembled in the meeting room for presentations by leading global printers on the latest trends in the packaging industry. These covered every corner of the field, from the latest trends in food packaging to plant design, global regulatory trends and more. Lively Q&A follow-up revealed the participants' expectations and concerns as well as their high regard for the presses they had just seen in action.
And finally there was a party, which went by in a flash as everyone was anxious to compare notes and hear the viewpoints of other packaging printers. The diversity of business models, types of printing, economic climates and outlooks on the future was sufficient stimulation to overcome language and all other differences. As the audience boarded their buses for the trip back to Tokyo, there was an additional comfort: the plum rains had stopped.
Lithrone GX40
Package Printing Perfection
High-speed automatic nonstop operation, lightning quick changeovers and makereadies, print quality meeting the demanding requirements of the deluxe packaging industry, and programmed task execution that ensures easy operation.
Six-color Lithrone GX40 with Coater, PQA-S and Extended Delivery
The cutting-edge Lithrone GX40 is the pinnacle of Komori technologies and expertise. In addition to extremely stable printing at the 18,000 sheets per hour maximum printing speed on sheets 0.06-1.0 mm in thickness, the Lithrone GX40 delivers both significantly improved print quality and enhanced agility for color changeovers. Everything needed to meet the extraordinary demands of package printing, including automatic nonstop operation and control systems to handle long runs at high speed, new washing/cleaning systems, and availability in special configurations for high added value work. The energy-conserving and space-saving design, along with reduced heat emissions, provides genuine benefits for the environment.
Additionally, the Lithrone GX40 can be configured with a stock transport logistics system. The automatic nonstop feeder and delivery are linked to this system, which transports stock smoothly through the printing plant. Resupply of the feeder and removal of printed sheets are automatically controlled and the flow of paper to the press is uninterrupted.
Powerful mechatronics systems
Orchestrating Lithrone GX40 operation is the Komori lineup of mechatronics products, starting with KHS-AI (Advanced Interface). KHS-AI is a print start-up and productivity improvement system that optimizes various presets by self-learning according to changes in the machine, environment and printing materials. With Smart Sequence, a near fully automatic makeready is realized. These functions shorten changeover and makeready times, reduce paper waste, conserve resources and significantly slash press downtime. Two powerful optional systems — the PDC-SX Spectral Print Density Control-SX Model and PQA-S Print Quality Assessment System for Sheetfed — are integrated with KHS-AI to provide a rich flow of data that raises the total level of print quality control and inspection.
Flexible configurations for high-end work
The mechanical design of the system is also optimized for package printing. Full-APC is standard, and the optional A-APC system may be specified to change plates on all units — regardless of the number — in just 85 seconds.
Unprecedented automation. Cutting-edge digital control. And a state-of-the art array of special features aimed squarely at the needs of package printing. The Lithrone GX40. The package printing press the industry has been waiting for.
Automatic nonstop feeder and delivery linked to a flexible logistics system that transports stock through the plant, PQA-S and PDC-SX — both integrated tightly to KHS-AI and offering ultra-high-spec options, and a programmed automatic blanket washing/roller cleaning system that offers an unprecedented level of performance. And this is just the start.
Nonstop Operation System
The nonstop feeder and delivery enable pile changing without operator assistance. Linked to a logistics system that transports stock smoothly through the printing plant, resupply of the feeder and removal of printed sheets are automatically controlled so that the flow of paper to the press is uninterrupted and high-speed printing continues until the end of the run.
PQA-S (Print Quality Assessment System for Sheetfed)
Using a high-precision CCD camera and lens, the system ensures in-line, high-level print quality control by inspecting all sheets according to the same criteria. The system checks for smears, ink splashes, water drops, oil spots, hickeys and color irregularities. It also prevents unacceptable sheets from continuing to be printed as well as unacceptable sheets from being mixed with good sheets that are sent to postpress. Tightly integrated with KHS-AI.
PDC-SX (Spectral Print Density Control-SX Model)
This system digitizes and automates control of colors, which were previously adjusted and controlled by the operator. In addition, an automatic register function enables the simultaneous measurement of both colors and register. In particular, the system greatly shortens the time needed for color matching and minimizes paper waste at print start-up by means of the KHS-AI-linked Smart Feedback function. Options include a PDF comparison function and a color correction function that enables accurate feedback of special colors using Lab values.
Automatic Washing/Cleaning System
Efficient automatic washing/cleaning by means of an automatic control program. The new automatic ink roller washing system significantly improves color changing, which is a bottleneck in printing with special colors. Moreover, program control means this system reliably washes out ink that has penetrated the pores of the rollers. This enables quick and accurate start-up of the next job even when changing from dark pigmented inks to light pastel inks. The use of a pre-soaked cloth for blanket washing and impression cylinder cleaning contributes to reduced cloth usage and provides benefits for the environment. Automating all these linked functions dramatically reduces overall makeready time.
Lithrone GX40RP
A Total Solution: Reverse Printing
One-pass double-sided printing with the optimum sheet path, single-edge gripping, and the full lineup of quality control technologies designed for its straight-printing stablemate, the Lithrone GX40.
10-color Lithrone GX40RP with Coater
Quality, efficiency and flexibility are the watchwords of the Lithrone GX40RP. Reverse printing — allowing both sides of the sheet to be printed in one pass with no flipping of the sheets and no need for tail-edge gripping. Available in either a paper or cardboard specification with either UV or H-UV curing. The simplicity of a straight press with the productivity of a perfector.
The H-UV/UV-equipped Lithrone GX40RP 40-inch dedicated offset printing press delivers high print quality, quick turnaround, high-speed stability, and reduced waste in one-pass double-sided printing. The reverse printing arrangement features single-edge gripping and eliminates sheet reversal. Single-edge gripping makes a margin on the tail edge of the sheets completely unnecessary, enabling stock costs to be cut by minimizing the sheet size. Configuration of four double-size transfer cylinders ensures stable sheet transport. Front/back plate imaging is in the same direction, just as with single-sided straight presses, increasing efficiency in prepress. The Lithrone GX40RP is available in two specifications: a thin sheet specification for commercial printing and publishing and a cardboard specification for package printing.
This machine can be configured with all of the basic systems and devices for ensuring quality that are designed for the Lithrone GX40. This means the press delivers cutting-edge short makeready thanks to the KHS-AI (Advanced Interface) integrated start-up control system and powderless instant drying with the H-UV/UV curing system.
Komori quality and a totally unique design. There's really nothing like it. The Lithrone GX40RP.
Komori-Chambon
Innovative Player in Packaging
Komori-Chambon was established in 1989 by the acquisition of Machines Chambon, a French company founded in Paris in 1887 that developed the original concept of printing and finishing systems for packaging. Today Komori-Chambon has emerged as one of the most distinguished players in the global packaging industry.
ORS-650
By assimilating Komori's 90 plus years of experience and expertise in manufacturing and press control technologies, Komori-Chambon benefited from a great infusion of automation technologies. This infusion resulted in web offset presses that deliver high print quality while allowing short makereadies along with reduced waste, higher output and efficiency, and thus greater profit potential.
Komori-Chambon is unique for several reasons. Komori is the only Japanese press manufacturer that operates a manufacturing facility in Europe. More importantly, Komori-Chambon is the only company in the world that offers web offset, rotogravure and combined process (including flexo units) presses with in-line finishing for converting paper, board and laminates. The company's headquarters and R&D department are located in Orléans, south of Paris, France, with a manufacturing facility in La Voulte, south of Lyon.
Lineup of flexible configurations
Two major lines of Komori-Chambon printing presses are well known throughout the packaging industry: the OR (Offset Rotary) range of web offset presses for liquid carton packaging and general folding cartons, and the GR (Gravure Rotary) line of rotogravure presses for paper, board and laminates with in-line rotary die cutter, platen cutter or label cutter. In the past few years, the company has also introduced the innovative OS (Offset Sleeve) series of sleeve web offset presses. All of these presses may be combined flexibly with a full set of optional technologies and added value processes, including hot stamping, hologramming, embossing/de-embossing, die cutting, stripping and label cutting. Delivery systems specialized to optimize production speed for many markets, including tobacco, liquids and fast food packaging. The benefit? The customer obtains a pile of finished product from a reel of paperboard. All product ranges boast access to Komori-Chambon's secret weapon: a near-limitless capacity for customized configurations.
The company is also a leading manufacturer of rotary die cutting and creasing tools for the packaging industry. These are often found in applications such as gable-top cartons for liquids. Employing a cassette system, the rotary die-cutting system uses twin knife, single knife or wrap-around plate die technology and may be installed with a matching stacker delivery on any web press thanks to an original independent drive system.
Komori-Chambon also manufactures an array of special machines for particular needs, including hot stamping and hologram presses configured with a rotary die cutter; rotogravure or web offset presses for in-line printing of stamps with perforating and numbering; and equipment for gravure or offset printing of tickets for mass transportation systems with in-line magnetic ink coating, numbering, encoding, and cutting or rewinding of tickets. In addition, a range of off-line finishing machines is available for the production of labels or cartons from preprinted reels of paper or board.
Komori-Chambon presses: the reference platform for quality and efficiency for the packaging industry.