On the Way to 500 Presses
Core driver of OffsetOnDemand: Komori’s H-UV technology a roaring success worldwide
01 December 2014
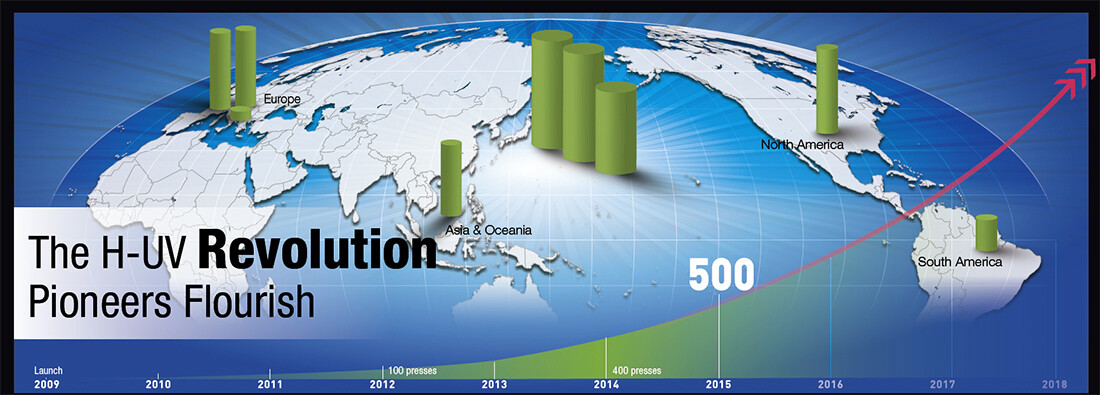
On October 6, 2009, Komori premiered the innovation that would transfigure printing — the H-UV Innovative Curing System, configured on an unassuming four-color Lithrone S32 at JGAS. This show set off a chain of events that is still unfolding, changing the very shape of the industry. Komori has done it before — with the development of fully automated plate changing 25 years ago, for example — and will do it again in the future. But the H-UV revolution that Komori has unleashed over the past five years is a unique, multidimensional transformation of the commercial offset printing industry that truly stands apart.
Developed by KGC, H-UV was adapted over the next few years to the leading ranges of Komori presses — the Lithrone S29 series, the A37 series, the G40 series in both straight and perfecting models, and the Lithrone GX40RP series in both sheet and cardboard specifications.
In February 2011, the Japanese Society of Printing Science and Technology presented Komori with the Technology Prize for its development of H-UV. And then in July of that year, Komori received the prestigious Printing Industries of America InterTech™ Technology Award. A few months later at IGAS and at drupa the following year, wider audiences saw the potential of H-UV and registered their approval with orders that rocked the industry. And in March 2014, Komori unveiled a 16-page System series web configured with the H-UV system. The rest is history.
As of September 30, Komori has shipped more than 400 H-UV-equipped presses. Indeed, these machines account for roughly 70 percent of total production of H-UV-configurable models. More than 150 installations overseas incorporate the H-UV system. Thus, now is the time to fill in the background to this extraordinary printing technology development and hear from the pressrooms and boardrooms of H-UV adopters.
Proven productivity powerhouse
By now, most of the Komori family is familiar with the essentials of H-UV technology: the energy output of a single H-UV lamp is precisely aligned with the required curing range of high-sensitivity H-UV inks. Much less electrical power is needed to dry the sheets and heat emissions are drastically cut. The visual pop and stunning effects expected from UV ink but with minimal dot gain, high ink gloss and true dot shapes. No powder spraying — and none of the troubles that often accompany this process. No ozone emissions and none of the odor associated with conventional UV. No 'dry back.' H-UV color doesn't change over time. Heavy ink coverage is no obstacle. Dramatic color effects on uncoated and matt stocks. And the ability to print on just about any substrate that will feed in the press — heavy stock such as cardboard, metallized paper, foils, and even plastic and film substrates that are susceptible to heat deformation with conventional UV.
But for printers, the biggest difference in the bottom line comes from the fast turnarounds of instant drying and the business growth that these many capabilities make possible. H-UV eliminates the compromises. As printing continues to evolve — with digital and inkjet playing a larger role and nanography beckoning on the horizon — H-UV has given offset, the proven bedrock platform of the commercial industry, a robust new lease on life. Just ask an H-UV user.
Forward Thinking Printing: Focus on H-UV
Printers, vendors and industry analysts gathered for a one-day forum intended to provide printers with the insights and inspiration needed to navigate successfully in the years ahead. The panel on the H-UV Innovative Curing System stood out as the highlight.
A panel discussion entitled "How H-UV is the new generation litho printing" was held on July 10 in London's Stationers' Hall as a part of the Forward Thinking Printing Forum. The event was devised to provide inspiration to the printing industry for the future.
Representing Komori were Steve Turner, Director of Sheetfed Sales, Komori UK; Uli Sause, Baldwin Technology's Key Account Manager for Komori; and Mark Plummer, Managing Director of Platinum Print — the first UK company to install an H-UV-equipped Lithrone.
Gareth Ward, Editor and Publisher of Print Business Media, chaired the event. He introduced H-UV as "new generation offset technology with a unique twist — providing benefits such as flexibility, immediate drying, reduced CO2 emissions and elimination of spray powder." Komori took the stage to explain the significance of the H-UV process in a discussion that drew the loudest applause of the day. The following is a selection of the questions tabled by the chairman and the responses from the three Komori panel members.
Gareth Ward: To start, I'd like to ask Komori UK's Steve Turner for the background to the development of Komori's H-UV process.
Steve Turner: At the outset, we started exploring ways of developing offset's core techniques to assist the printer in attaining faster all-round production speeds, primarily as a response to the accelerating print-on-demand market. The limitations of classic UV, which, while enabling quick drying, also uses considerable power and emits ozone and heat, were never ideal in a commercial print environment. So we researched alternative drying techniques that captured the upsides but eliminated the downsides of conventional UV. This was the approach in Europe.
GW: Mark Plummer, when you installed your four-color Lithrone S29, you were the first in the UK to acquire the H-UV process. Why did you go down that route?
Mark Plummer: I had 25 years' background in production at Platinum Print, and I became acutely aware of just about every production issue that could arise. Now, as MD, I had to answer the question, how do we grow the business and maintain delivery promises and quality when we can't calculate precisely how long jobs will take to dry?
GW: How has H-UV been for you so far?
MP: Very good. As with all new technologies, you have to adapt to the differences such as plate handling and production scheduling, but we turned the corner very quickly.
GW: Steve, what's been driving the interest in the H-UV process and where is it strongest?
ST: As of today Komori has received orders for more than 400 H-UV presses around the world, with sales initially to printers in Japan. There, printers tend to use uncoated materials and are limited by minimal floorspace to accommodate slow-drying sheets. Now 70 percent of new Komori presses sold in Japan are H-UV equipped, and in Europe it's already approaching 50 percent. What's driving this? Basically, whatever the material being used, the inks cure so fast that the sheets can be taken immediately to the next process, whether that's reverse side printing or finishing. The quality is excellent, and the feel of the sheet is smoother since there's no spray powder. So turnaround is faster, the work is better, and the production costs are lower!
Interestingly, in Europe now, the enhancements that the H-UV process can facilitate are proving increasingly popular, with fifth units and also coating units being added specifically to provide added value finishes such as drip-off, high gloss and spot varnishing. In France, for example, over 50 percent of H-UV-equipped presses have such specifications.
GW: Uli Sause, your company, Baldwin Technology, worked with Komori in the U.S. and Europe to develop the H-UV lamp. What path did that development take?
Uli Sause: Looking back at classic UV, traditionally systems would be installed as additions to standard presses. Usually this would be on highly specified presses and mostly for dedicated packaging applications where the inherent characteristics of higher dot gain, the requirement for a series of interdeck UV lamps, ozone extraction systems and significant heat generation were accepted and could be cost-justified in that sector. Like Komori, we saw the need for a fast drying system that would be suitable for the commercial offset market. From the start, we both recognized that this meant creating a new process, not just an adaptation of existing products. So we engaged closely with Komori and carefully chosen consumables manufacturers to find the optimum cost effective, environmentally conscientious solution. That combined research is what finally created the H-UV process.
GW: Steve, any comments?
ST: I agree. Fast drying was the primary aim, but certainly not the only one. In addition to improving the environmental side, in particular no heat or ozone generation, and keeping running costs low, we wanted a process that ensured stable color. With the H-UV process, the color you see on the sheet in the delivery is exactly the way it stays.
GW: Mark, how does all this affect your business?
MP: In the past, on most jobs, we made an allowance of an hour pass time to verify the sheet. Now it's instant, even on work with high ink densities and on uncoated or any other materials. And, additionally, there's greater sharpness of color than on jobs printed without H-UV curing. We have no partly dry sheets lying around, and that makes for greater efficiency on the shop floor.
GW: Steve, what about costs?
ST: Several aspects to mention here. First, there's only one lamp required on a straight press, whatever the size or configuration. And only two on perfecting presses — one after the first set of units and, as with straight presses, one in the delivery. So the initial cost and the power used are both lower than with classic UV. Second, except for added value purposes such as special effects and spot varnishing, there's never a need to specify further units or coaters for the purpose of sealing or aqueous coating. So the capital outlay is minimized. Power consumption is appreciably lower, too.
GW: But what about the inks and their costs? Uli, would you like to answer?
US: The required density levels are lower with H-UV inks. With H-UV, the ink sits on top of the paper, and as a result you achieve a higher optical density with the same amount of ink, or, alternatively, require less ink to achieve the same density when compared to standard inks. So you achieve more with less!
GW: Do the inks need photoinitiators?
US: H-UV inks polymerize in the same way as standard UV inks. The difference with the H-UV process is that the reactive components and the lamp output are matched to increase efficiency. In addition, the photoinitiators have been further developed to give multifunctional properties such as a higher molecular weight and therefore are less likely to migrate.
GW: What about metallics and other consumables, Steve?
ST: No problem with metallic! And we're proud to say we're prescriptive about what key consumables the printer uses — inks, blankets and fount solutions — so we can give a total commitment that the H-UV process will always deliver!
GW: What about recycling of paper printed through the H-UV process?
ST: In fact, it's simpler, because the H-UV ink binds as a film on the surface of the paper, meaning the ink separates from the paper more easily.
GW: Uli, what about lamp life?
US: The H-UV lamp material and filling are very special. Of course, the lamp is a consumable, but Komori and Baldwin give a substantial warranty on the time the lamp will function at maximum effectiveness. Replacement is also easy and quick.
GW: We've not discussed LED yet, Uli. Would you like to comment?
US: LED works over a very narrow wavelength so operational tolerance is limited. LED inks require a very targeted narrow band of radiation. When the required wavelength is missed or is blocked, there's a minimal curing effect! Current LED systems are monochromatic, which means that only a narrow band of UV light is emitted. It's difficult to formulate the ink as only a small selection of photoinitiators reacts in the area where the LED emits. Secondly, the pigments in the inks absorb UV light — at the same time reflecting visible light — so there is an inherent conflict between the photoinitiators that require UV for the curing process and the pigmentation that absorbs the radiation. The broader range of H-UV does not have this issue. The wider range of photoinitiators available for H-UV inks and coatings gives certain properties to the ink and coating that currently cannot easily be addressed by LED because the suitable wavelengths are not available. LED clear coats still tend to change color and go yellow after exposure to LED UV.
On the other hand, UV inks, such as those used in the H-UV process, operate over a wider wavelength band, and so the ink formulation can incorporate a large variety of different photoinitiators with different properties that ensure complete curing without tainting.
GW: Steve, what about H-UV on perfecting presses?
ST: On perfecting presses, H-UV curing has its own further set of benefits because the first side is completely dry before the reverse side is printed. So, for four-over-four work, no fifth unit is required to carry machine sealers. On the reverse side of the sheet, no white space needs to be allotted for sheet transportation, so smaller sheet sizes can be utilized and full-out images can be carried on both sides of the sheet. These advantages mean more flexibility with design and pagination.
With H-UV curing on perfecting presses, no ceramic jackets are required, thereby ensuring that color representation on both sides of the sheet is a precise match. Additionally, there are no jacket replacement costs or subsequent loss of production while jackets are being replaced.
GW: A final word from you, Steve?
ST: We've said a lot about Komori H-UV here, but what stands out to me as the continuing theme on the other presentations here today has been the need for printers to have something to market, something which differentiates them from other printers.
The Komori H-UV process provides exactly that.
Note: Figures are as of July 2014.
Equipment/materials differ by area and are localized by testing/verification.
"As MD, I had to answer the question, how do we grow the business, maintain delivery promises and quality when we can't calculate precisely how long jobs will take to dry?"
—Mark Plummer
"With H-UV, the ink sits on top of the paper, and as a result you achieve a higher optical density with the same amount of ink"
—Uli Sause
"So turnaround is faster, the work is better and the production costs are lower!"
—Steve Turner