Dusung makes waves with Korea's first Lithrone GX40RP
Korea, Dusung Print | Lithrone GX40RP [GLX-840RP]
01 March 2016
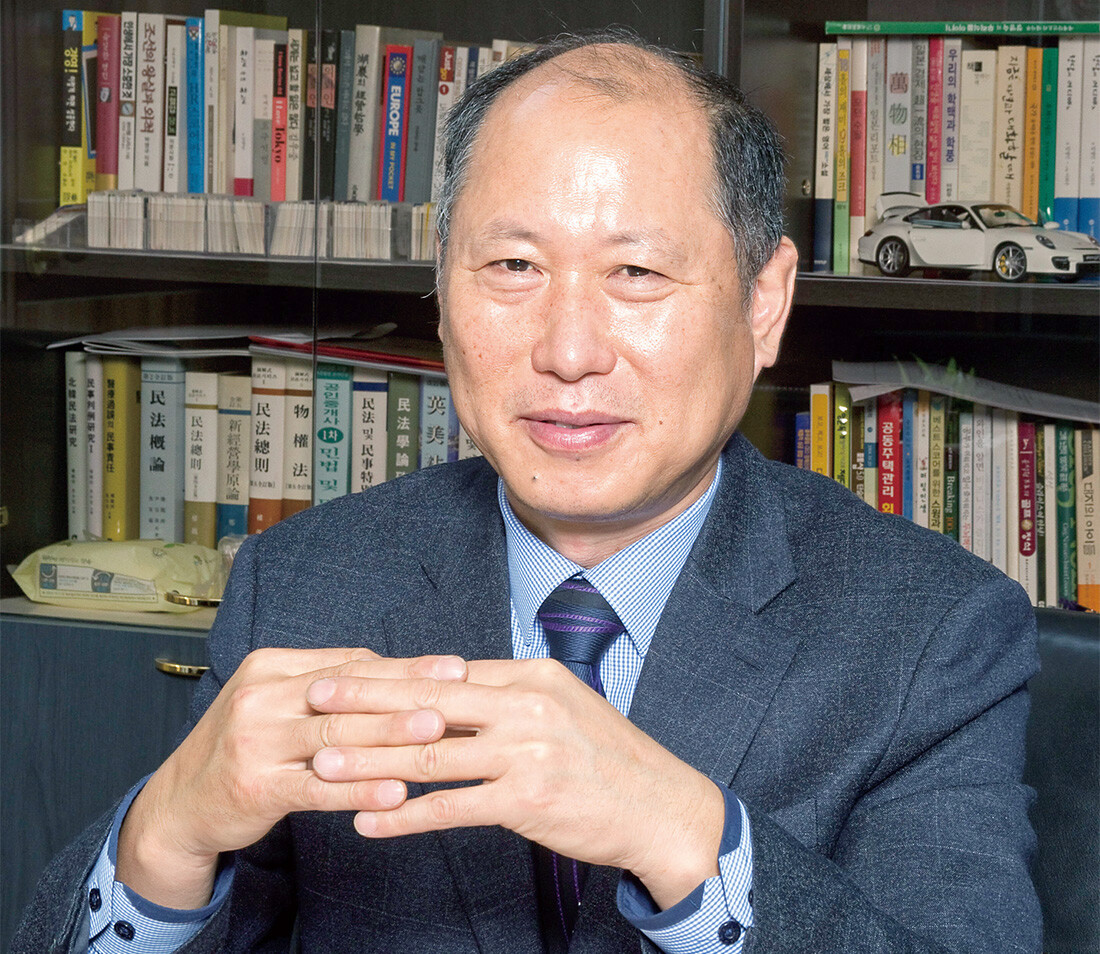
The densely populated capital city of Seoul holds more than 20 percent of the Korean people. Recently printers looking to expand have been moving from Seoul to nearby satellite cities to reduce costs. Going against this trend, one printing company located in the center of Seoul installed Korea's first eight-color Lithrone GX40RP.
Kim Sang-gyu, Representative Director
Dusung finds the solution: Komori
Kim Sang-gyu, Representative Director of Dusung Print, launched a printing business called Yujin Culture in 1991. Starting out with a used four-color Lithrone 26, the company eventually built a fleet made up of a five-color Lithrone S40, a five-color Lithrone S26 and a four-color Lithrone A37. Lee In-kyung, in charge of company finances and management, describes Dusung's partnership with Komori: "Although for a while we were running presses from another manufacturer, frequent machine breakdowns and printing difficulties were extremely troubling. Other printers we knew recommended Komori machines, and once we installed a Komori press we were free of these problems. We love Komori."
Dusung Print's main customers — fashion houses famous in Korea such as Joinus, HUM and Beanpole; jewelry brands Goldendew and Stylus; and ad agencies like Born Creative and ADline — make up 90 percent of the clientele, so print quality is Dusung's lifeline. And for this reason, selecting printing presses with a view toward quality is crucial to the company.
'First in Korea' press: big news
In August 2015 Dusung Print installed the eight-color Lithrone GX40RP — the first RP type duplex press in Korea. That an ordinary printer running three presses in Seoul had decided to invest in this press was big news in the Korean printing industry. Director Kim explains why: "A breakthrough was necessary to maintain our competitive edge in price and orders compared with the small printing companies that remain in Seoul. And we also paid attention to firms printing large volumes of work who had moved out of Seoul. We believed that we stood a good chance of prevailing if our productivity and competitiveness were up to the task. That was when we noticed Komori's RP type duplex press." Mr. Kim spent one year studying all types of double-sided printing presses and visited Japan twice to observe the RP: "My research convinced me that the Lithrone GX40RP was the preferred choice. With both the conventional double-deck and long perfector types, there were limits on the paper thicknesses that could be printed, and there were issues both with print quality caused by the use of leading- and tail-edge grippers and with paper waste. The GX40RP, however, was a perfect double-sided press that had overcome these shortcomings."
Kim gives a rundown of the smooth installation process: "While the machine was being manufactured, preparations for moving the factory were being made. In general, finding a factory to accommodate a machine more than 25 meters long is so difficult that people asked us whether any place in Seoul would have room for a Lithrone GX40RP. Fortunately, we found a 1,650-square-meter factory that was close to our original facility. The space allowed us to run our earlier five-color Lithrone S40 and five-color Lithrone S26 in the same premises."
Flying colors in first test
The introduction of the machine proved extremely gratifying. No sooner had the press been installed than the printer had an experience that exceeded his expectations for the Lithrone GX40RP: "Right before installation, we got an order from a client for one million sheets of double-sided work in 40-inch format. With a one-sided machine, that would have been a job requiring 17 to 18 days working day and night — printing one side, drying, flipping the sheets, printing the reverse side, drying and finally delivery. Even though it was still in the setup stage, the RP was running at its awesome 16,500 sph printing speed, and the job was completed in just seven days. I saw with my own eyes that productivity had more than doubled. And there were absolutely no problems of set-off during printing and no scratches or feeder stoppages."
"This press really shows its power in short-run work. It is specified with a full complement of automation, including A-APC, KHS-AI and PDC-SX, so there is no waste in job changeover or during a production run. When running 500-sheet jobs, its productivity was sufficient to finish 10 jobs per hour. The CTP system can't even keep up," he says with deep pride.