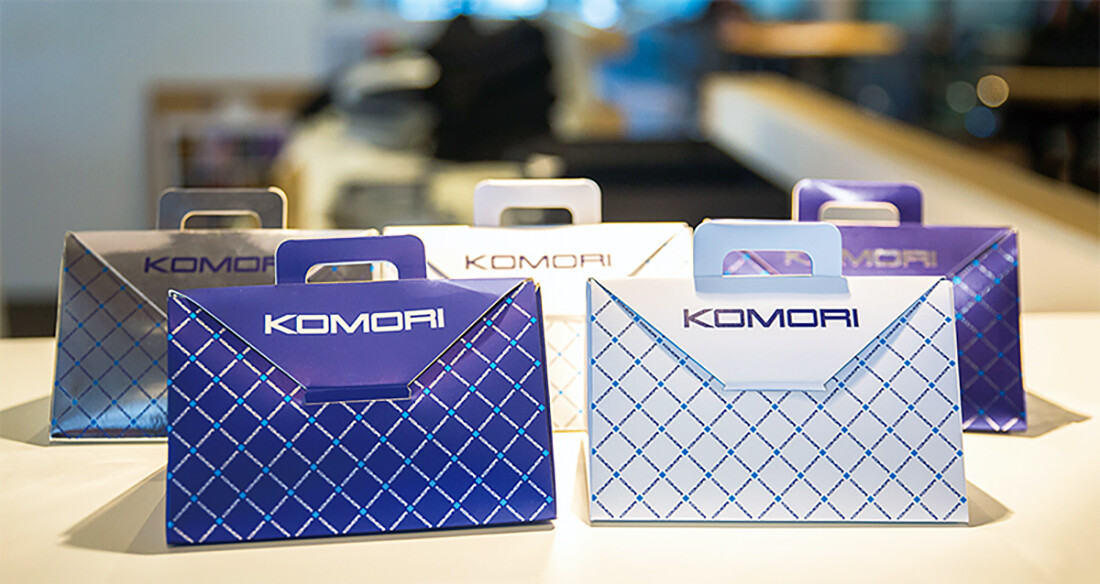
In January 2015, Komori launched sales of the Apressia CT115/CT137 lineup of programmable hydraulic clamp cutters. In September of that year, Komori's postpress initiative got under way in earnest as the Apressia DC105 Automatic Flatbed Die Cutting and Creasing Machine was shown at IGAS 2015. This postpress lineup was augmented with the addition of the Apressia CTX series cutting system equipped with an automatic paper transport function in September 2017, and the Apressia MB series blanking system will be added in early 2018. So why is Komori — the leading printing press manufacturer — devoting its energies to postpress? On Press asked Shigekazu Inoue, Section Chief of the Equipment Business Promotion Section of the PESP Business Promotion Department.
No solutions without postpress
- What is the background to Komori's full-fledged postpress initiative?
"There are many types of printing — publishing, commercial, currency, forms and packaging — and demands for high quality and short turnarounds are increasing throughout the industry. And printers are striving to meet these needs. By adding solutions for increasing production efficiency to its lineup of offset presses and digital printing systems, Komori is providing solutions to these issues. Although replacement and standardization of prepress equipment and presses are under way, issues persist in the postpress space."
- What sort of issues? Why is postpress lagging?
"Postpress work does not begin until the previous process, printing, is complete, and since process control varies according to quantities and types of products, postpress is most affected by the demand for short turnaround. Securing enough manpower is also a problem since there are so many uncertain factors. Also, since investment in equipment has often been put off, finishing machines that are 20 or 30 years old are still in service, and some production sites still have quality control that consists of personnel inspecting one item at a time. Moreover, there are so many types of printed products that the processes — cutting, binding, cropping, laminating, foiling and so on — differ with each product. Standardization is easy when the work is regular and runs are long. Many packaging jobs, however, consist of short runs. Thus, for these reasons, postpress standardization and digitalization are not keeping pace. The result is a bottleneck for the entire production process. Since standardization and digitalization of presses has progressed, Komori understands that now is the time to work on postpress standardization."
- What is necessary to solve these fundamental issues of postpress?
"Automatic equipment will take care of manpower shortages and help in production synchronization by shortening the process and turnaround time. With standardization and digitalization, we will improve operational efficiency and quality. To really ensure greater efficiency, though, it is necessary to think of the entire flow from prepress to press and postpress. Making press more efficient is meaningless if there is still a bottleneck in postpress. Printers need a fulfillment setup, and Komori has decided to provide total support based on this idea. This is the reason Komori has tackled postpress. Komori has been working on press automation for around 30 years. We intend to incorporate the know-how gained and also opinions from the plant floor in the manufacture of postpress equipment that is easy to operate."
Komori quality embedded in all our finishing solutions
"Komori first developed the Apressia CT series of programmable cutting machines to provide solutions in this sector because many printers, who handle both light and heavy stocks, as well as packaging producers require this equipment. We followed this up with the Apressia DC series of die cutting machines for package punching and die cutting, and in September 2017 the Apressia CTX series cutting system with automatic paper transport functions was added to the lineup. In early 2018 Komori will launch the Apressia MB series for blanking die cut paper."
"Although not a Komori brand product, Komori and its subsidiaries in the U.S. and Europe offer the Highcon Euclid III Digital Cutting and Creasing System from Highcon of Israel. This further expands our solutions for postpress and enables cutting and creasing without the use of a cutting die. The Highcon line adds a whole new level of options in finishing."
- What are the distinctive features of the Apressia CT series and the Apressia DC105?
"The Apressia CT series of programmable hydraulic clamp cutters are equipped with a 19-inch touchpanel that affords easy operation. With a working space of 735 mm from the knife to the edge of the table, ease of use is exceptional. Boasting the fastest speed of any product in this class, the Apressia CT machines have outstanding productivity on packaging work with many cutting processes. Having many densely arranged air nozzles, the air table improves the handling of sheets for cutting. Because there is no transport belt for back gauge movement, there are no paper problems or smudging. The Apressia DC105 flatbed die cutting machine has sheet feeding and delivery, die cutting and trim stripping as standard functions. The sucker box, in particular, provides stability with both light and heavy stocks due to the use of Komori sheet feeding technology. Equipped with a semiautomatic pile splicing mechanism, this machine is exceptionally effective with long runs and paper changes due to the nonstop feeder and delivery. The operating buttons and touchpanel display on the register integrate the front lay and side lay fine adjustment functions and ensure very good operability."
Komori postpress strengths
Apressia lineup debut at IGAS 2015
- You mentioned that the know-how gained in press manufacturing is used to full advantage in making postpress equipment. What other strengths does Komori bring to the table?
"One strength is that Komori as a maker, unlike a trading house, reflects the demands of the production floor in product manufacturing. When we rolled out the Apressia series at IGAS 2015, we heard surprise at the idea of a Komori postpress lineup. We also heard, however, a great deal of advice on improving things. And Komori listened. Paying attention and actually making improvements is one of Komori's biggest strengths."
Not just machines
• High cutting accuracy due to solid construction
• Range of automation and labor-saving options
• Compatible with CIP3/CIP4 and KP-Connect
• Peripheral option system for varied issues
- What is the picture of total support by Komori, now that the company has stepped into postpress?
"Our goal is to present bold proposals for the total process — for prepress, press and postpress, from receiving orders to shipping products. Although the flow of materials between processes is still in the future, eventually we will develop a system that compacts and disposes of paper scrap. To meet the needs of our customers, we will also develop an array of finishing systems and integrate them with standard control technologies. For this purpose, we will cooperate with a variety of other makers. When partnering with other manufacturers, we intend to provide assistance in customization and utilization."
"In addition, because Komori is building our own factories, we have extensive factory planning and design know-how. With many decades of experience as a press manufacturer and based on relationships with many printers, Komori is thoroughly familiar with on-site issues and issues between processes. We study these every day. With this experience, we believe that we can make very significant contributions not only in suggesting equipment but also in constructing new printing facilities."
- Finally, what is the outlook for the future?
"With Apressia CTX, we have reached the stage of achieving cutting machine automation. For the work of managing paper in heavy-duty cutters in postpress, automation is indispensable. Automation is also critical for improving the workplace environment and securing manpower, so Komori will continue to make every effort to meet the keen demand of printers for end-to-end operation and control of prepress, press and postpress. No matter how strong a lineup of postpress devices we develop, it will only be meaningful if printers actually develop business that uses the equipment. And that is why we will also propose business models for each postpress machine. Printers install presses and postpress machines to address specific business issues and solve outstanding problems. Komori makes finding solutions for printers' issues its number one priority. We're listening."
Sales of postpress machines differ by area.