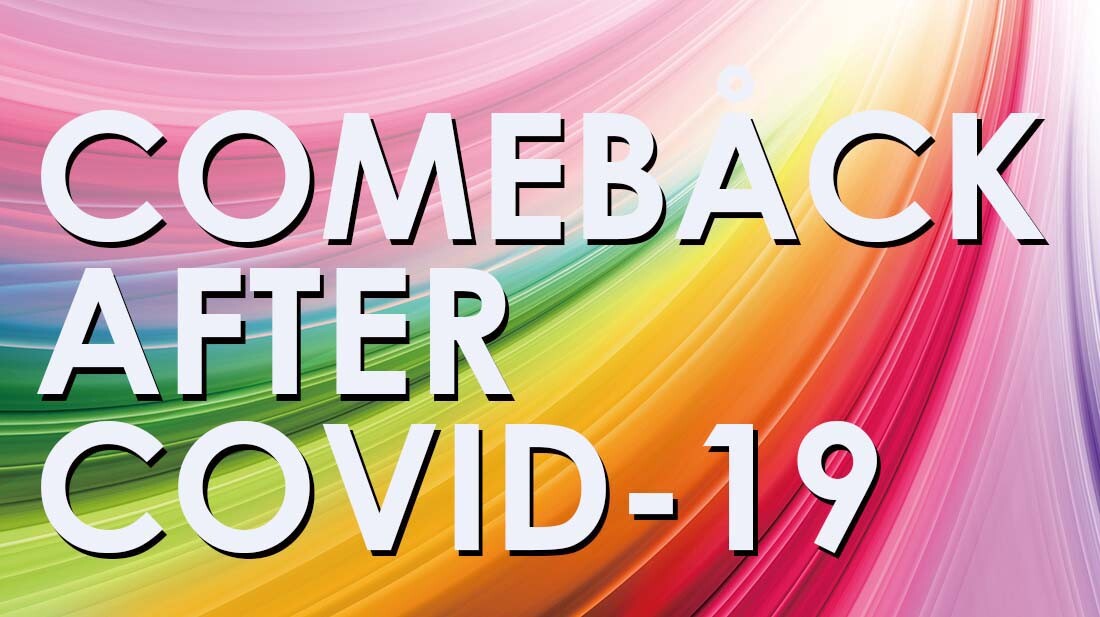
To restart the economy after the prolonged Covid-19 pandemic, efforts are under way in countries around the world to restore demand through monetary easing policies. On the other hand, two changes accompanying the economic recovery are expected to make it increasingly difficult for manufacturers to remain profitable.
First, stagnation of production due to the spread of Covid-19 infection, especially in Asia, has disrupted the supply chain, and inflation due to the supply-demand gap has begun to emerge. In addition, there is a fear of a further rise in the cost of materials and energy due to the rapid implementation of environmental measures and to heightened geopolitical risks.
Second, moves toward improving the working environment, including reforms in the way people work, are expanding globally. Companies must respond with increased wages and restrictions on working hours. Furthermore, as each individual reevaluates his or her work style after Covid-19, it is expected that labor-intensive manufacturing industries that focus on simple tasks will have a harder time attracting workers.
In this environment, Komori believes that companies need to restructure production systems and radically raise productivity to secure profits. In this feature article, we focus on commercial printing and will introduce double-sided printing solutions to improve productivity.
Changes in the global labor environment and need for improving labor productivity
[Figure 1] Change in average annual wages in major countries
[Figure 2] Change in labor productivity in major countries (GDP per employee)
Looking at the global labor environment, average wages in major countries continue to rise year after year. [Figure 1]
Companies in these countries have been aggressively investing in capital equipment to improve productivity in order to keep pace with the annual increase in wages. This is backed up by the increase in labor productivity (GDP per employee) in major countries. [Figure 2]
As noted at the beginning, there is a risk of a further surge in inflation due to supply chain disruptions and other factors. To cope with this, it is necessary to implement a bold review of the production system and increase production efficiency.
South Korea has already faced these issues. In South Korea, economic policies to reform work styles and redress wage disparities have been in effect since 2018, and major changes have been made, including restrictions on weekly working hours, overtime regulations, and a 42 percent increase in the minimum wage in the short period of five years. For companies to respond to these severe policies that are putting pressure on profits, the printing industry is aggressively investing in equipment to improve productivity. In commercial printing in particular, there is a growing trend to improve productivity by replacing single-sided presses with double-sided presses equipped with the latest automation technology. Shipments of double-sided presses have increased rapidly, and in 2021 were 2.5 times greater than in 2018, the year the policies were launched. Komori presents a case study of a rapidly growing South Korean web-to-print (W2P) user that introduced Komori's latest double-sided press and the company's response to changes brought about by IT-driven automation.
Double-sided one-pass production generates significant profits
Most commercial printing is double-sided, but many printing companies use single-sided presses to print the front and back in two runs. This method requires more manpower and time because in addition to printing twice, there are the processes of paper reversing and reloading and, in the case of oil-based printing, waiting for the paper to dry. On the other hand, many customers may have chosen to use single-sided printing presses because of the capital investment and installation space required for double-sided printing presses. However, the latest double-sided presses offer a much higher return on investment (ROI) due to their improved basic performance and automated functions. For example, under certain conditions, when three existing oil-based 4-color single-sided presses were replaced with one new 8-color Lithrone G37P advance LED-UV double-sided press, the estimated profitability shows that it is possible to obtain greater production capacity than before and a gross profit on sales (*1) that is about 1.7 times that of the three single-sided presses. (* 2)
Such "downsizing" to consolidate the number of machines by installing the latest, most productive presses, while maintaining production capacity, can significantly reduce operating costs, including labor costs, maintenance costs, paper waste, and power consumption. Furthermore, major process changes such as these can lead to support for reforms in work styles, environmental issues, and SDGs. Implementation of this business model change can be seen around the world and the results are always the same, proving the need for the commercial print market to move to a double-sided print production model in order to raise productivity and secure profits.
*1. Gross profit on sales less cost of goods
* 2. Effects of introduction and improvements noted here are measurements and estimates under certain conditions provided as information for reference in investment decisions and actual effect are not guaranteed.
Three types of double-sided printing presses to meet every need
[Figure 3] Positioning of work characteristics and main double-sided printing presses
Commercial printing involves a wide range of work, and the functions required of printing presses differ.
[Figure 3] shows the positioning of Komori's double-sided printing presses, with lot size on the horizontal axis and work characteristics on the vertical axis. The work characteristics are positioned as efficiency-oriented when double-sided printing accounts for the overwhelming majority of jobs, and as flexibility-oriented when both double-sided printing and single-sided multicolor printing are used.
Next, the structure and features of each type of double-sided press are introduced.
[Figure 4] Three types of double-sided printing presses
• Perfecting press (P type)
Example: Lithrone G37P advance and Lithrone G40P advance
The P type press (commonly called a convertible perfector) can switch between double-sided and single-sided printing. This allows for flexibility, such as single-sided printing with multiple colors in addition to double-sided printing. One consideration for the P type press is that the printable area of the sheet is slightly reduced because of the need for gripper area on both the lead and tail edges of the sheet. Furthermore, there is a remote possibility of front-to-back register inaccuracy. Komori's portfolio includes 37-inch and 40-inch perfecting presses, with the 37-inch model being best suited for specialized printing of A4 sheets with an 8-page imposition. The press's compact size reduces running costs such as printing plates, paper, and power consumption, resulting in high profitability.
The 40-inch press can handle irregular sizes up to 40 inches, making it suitable for a wider variety of jobs.
• Dedicated double-sided press (RP type)
Example: Lithrone GX40RP advance
Dedicated double-sided machines (RP type) are specialized for double-sided printing. Since there is no gripper change from the leading to the tail edge of the sheet, the machine offers high precision with no possibility of marking the sheet. Because the process only requires gripper area on the lead edge of the sheet, the printable area can be maximized, keeping imposition efficiency high and costs low. The Komori RP type press is the most efficient way to print on both sides of the paper, making it ideal for customers who want to increase production volumes regardless of lot size. Komori's portfolio includes 40-inch and 44-inch RP press sizes, and the 40-inch model is available in an 18,000 sph high-speed specification.
• Oil-based double-sided press (SP type)
Example: Lithrone S40SP
The SP type is a press specialized for oil-based double-sided printing. By eliminating the transfer cylinders and directly connecting the impression cylinders, the overall length of the machine is shortened, making it possible to install a double-sided press even in a limited space. Like the RP type, the SP type uses a single-edge gripping system, making best use of the printable area of the sheet. The SP type is suitable for customers who have factories in urban areas or areas where large factory lots are not available. It also caters to customers that have work such as publication printing of single- or two-color books, or instruction manuals.
Komori takes pride in being the only printing press manufacturer in the world offering a lineup of three types of double-sided presses in multiple configurations. This allows Komori to use a consultative approach when providing the ideal proposal matching the characteristics of each customer's work mix.
Truly useful automated technology that realizes easy operation by insourcing
The advance series of offset presses, introduced in 2020, are the latest printing presses with enhanced automation and digitalization functions designed from the beginning to address the shortage of skilled operators, one of the most challenging hurdles faced by the printing industry today. Komori's press concept is easy operation that is designed to minimize the need for skilled labor. The machine has been designed to perform the task of simple and quick color matching, where individual differences due to skill or experience are common, reducing the need for human input. In particular, Komori press controls use a complete system consisting of the self-learning KHS-AI print operating system, PDC-SX spectral density control system for accurate color reproduction and PQA-S for color control automation on-the-run, providing optimum overall performance. Color control with fast and accurate feedback enables maintenance of stable color even at high printing speeds. Operators at the press site say that this reliable color control allows them to increase printing speed to the maximum, with confidence.
Advanced feedback control technology has also made autopilot automatic operation practical. The press provides full support for register and color adjustments for test printing and OK sheet confirmation, processes originally requiring skilled operators. The press operates automatically until the end of production printing without stopping for trial sheets, allowing the operator to concentrate on other tasks and realizing one-man operation of the entire press.
The advance press series also incorporates various types of automation and remote-control systems in its complete pursuit of easy operation that anyone can easily manage. Amid the increasingly severe shortage of human resources, we are confident that our advanced state-of-the-art machines will contribute to an environment where a broad range of labor is available to operate the press.
Digitalization and robotization of postpress processes eliminate bottlenecks throughout the entire printing plant
Production changes are not only needed in the pressroom area. Postpress production is also in need of process change to remove the bottlenecks of older work flows. Postpress processes are generally labor-intensive, requiring a lot of heavy labor and simple tasks such as palletizing that require a great deal of manpower and time. With the current difficulty in securing human resources, now is the right time to introduce automated machines and robots/cobots.
Komori offers a lineup of automated and digitalized products to increase postpress productivity.
For example, the Apressia CTX cutting system automatically programs and presets the cutting process, allowing even inexperienced operators to work with efficient cutting processes. In combination with various automation devices such as lifters and joggers, this reduces the heavy workload of handling paper and enables a single operator to perform what has been a two-person job.
In the folding process, automatic palletizing of the finished product using a cobot, eliminates manpower shortages and dramatically speeds up production rates. The use of a collaborative robot (cobot) allows the machine to integrate easily next to the existing human labor force and it is safe without a cage. The folding speed can be increased because the operator no longer has to attend to the task of stacking signatures on a pallet. The cobot can always keep up, and it never has to take a break or go to lunch. Replacing the manual delivery with an automated cobot will enable the introduction of a high-performance folders and dramatically improve productivity. The MBO CoBo-Stack palletizing cobot supports high-speed folding at folder speeds up to 275 mpm, matching the MBO K8-RS High Speed Folder specifications. The technology removes so much operator labor from the process that a single operator can run two high-speed folding machines.
To help manage the new high-speed production and keep the work moving efficiently, with minimal downtime and maximum factory efficiency, Komori provides KP-Connect Pro middleware, which enables real-time monitoring of the operating status of all equipment along with centralized management of the production schedule.
To secure profits from commercial printing in preparation for major post-Covid-19 changes, the key solutions are to improve productivity by shifting to double-sided one-pass printing and implementing digitalization and automation of postpress. Komori provides these fully automatic solutions and more.
Click to see case studies of users succeeding in commercial printing