Packaging in Focus: Komori's State-of-the-Art Solutions
Packaging Solutions
01 March 2017
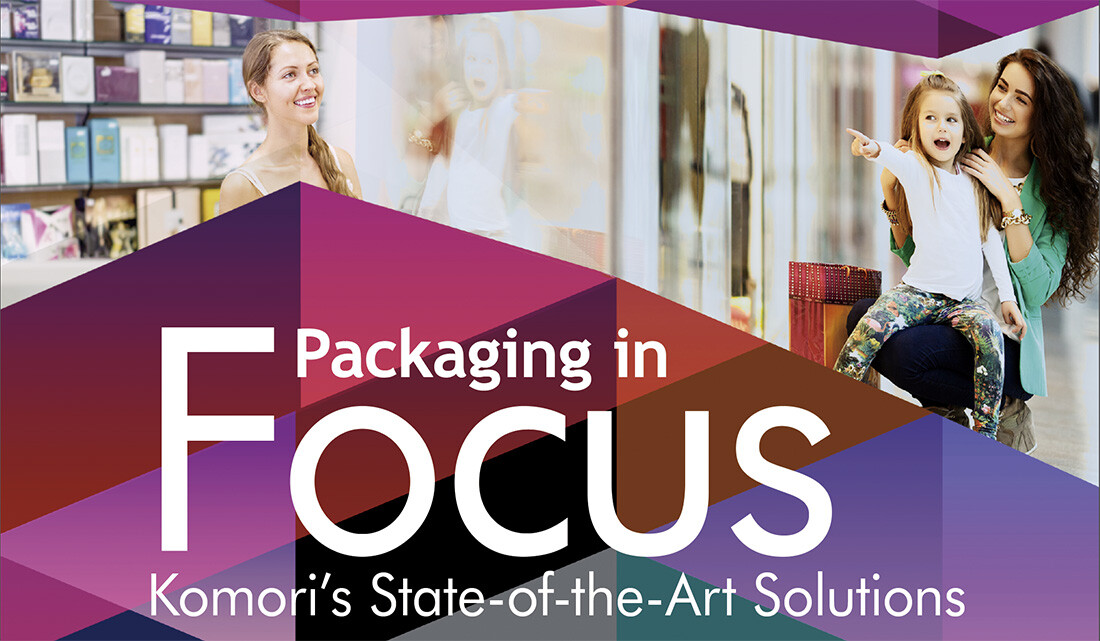
Packaging OnDemand: The Komori strategy supreme
Packaging is integral to virtually every product in the marketplace for many very good reasons. The package protects the product in every phase of shipping and distribution and communicates to customers the brand identity and other product specifics at the critical moment: point of sale. Packaging is the face of new products, conveying to the target consumer a carefully crafted message and tactile feeling that offer shelf impact and raise brand awareness. The packaging printer must deploy container design expertise and high quality multicolor printing capabilities on every substrate imaginable to succeed in a space that grows more competitive by the day. The challenges are daunting and the rewards by no means certain. Fortunately Komori is on hand with proven solutions.
The Komori tradition of invention
For decades, in fact, Komori R&D has produced many of the most important advances in printing, innovations that are now taken for granted. In 1984, for example, the world's first inline coating unit was developed and introduced to the printing world by Komori. During a period of great change in machine hardware, when the basic configuration of the modern offset press enabling multicolor and double-sided printing was being determined, Komori was the first to lay out a roadmap for package printing that incorporated an inline coater.
Just six years later, at drupa 1990, Komori stunned the printing industry again by announcing the world's first fully automatic plate changer — a breakthrough so advanced that competitors were deeply skeptical at first. Now Full-APC is SOP for everyone.
Also in the 1990s, short makeready for quick print start-up with the minimum amount of paper waste emerged as the most pressing need for printers. Komori introduced the KHS instant print start-up system, an innovative solution that presets the ink fountain keys during changeover. This too revolutionized printing. The entire process picked up speed. Now, further developed as KHS-AI, this system is the world's undisputed leader in print start-up technology.
Digital in sight
The environment of the printing industry is ever changing, and the printing market inevitably responds to economic changes and market needs. One such response is the emergence and growth of digital printing. Meanwhile, as commercial offset keeps pace with a greater variety of jobs, package printing is seen as a promising field. And Komori is once again leading the industry, rolling out digital printing systems and originating offset solutions tailored for packaging.
Needs established: solutions ready
The market needs driving package printing and the solutions meeting those needs are unique. The printing market in general does not admit of easy reassurance. Needs are becoming more stringent and competition is growing ever more intense. The most urgent requirement for staying in business is lower production costs. And the key to this is shortening production time and cutting paper waste. Precisely the areas where Komori excels: printing press automation and short makeready.
Getting color right is, of course, fundamental. In package printing the use of standard densities and color standardization were considered extremely difficult to implement. Typically printing samples and proofs were essential to getting color in package printing in the past. But in recent years the move to standard densities and color standardization has grown quickly. The background to this is, of course, large clients who comply with ISO-based standards for their own products, thus leading to the general demand for standardization in the industry.
Additionally, color adjustment must be comprehensive, covering highlights, shadows and intermediate tones. More than anything, it is very important to recognize that printing with standard densities is the easiest and most productive way of working. And KHS-AI, based on standard density targets, is the optimum system that provides powerful backup to this strategy of printing.
The shortest color adjustment time in the industry, however, cannot be attained by digital control alone. It is rather the result of combining digital control with the highly accurate ink key system, the unique Komorimatic continuous dampening system and a finely controlled servo-driven impression on/off system.
The Lithrone GX40 packaging dream machine
The illustration above shows a seven-unit Lithrone GX40 configured with an abundance of possible options developed by Komori as solutions to the three main challenges facing package printing: production cost reduction, quality control and high added value. The feeder is specified here with a full lineup of quality control devices: the new single suction tape feeder, automatic double sheet detector and sheet misalignment detector, all helping to ensure that sheets are fed with complete precision. An exhaustive complement of mechatronics systems and devices — KHS-AI V6, PDC-SX, PQA-S and the Komorimatic dampening system, to name a few — make sure that every sheet of paper, dot of ink and bit of data are in exactly the right place at exactly the right moment. Komori's advanced PDF Comparator System, optional with PDC-SX, scans the printed image for comparison with the originating PDF file data, allowing the operator to check for missing or anomalous characters in the initial printing stage and thus preventing production losses.
Special for Lithrone GX40 Series
Features that are particularly suited for packaging are integral to the Lithrone GX40. In addition to air and register presets, KHS-AI provides strengthened linkage with PDC-SX and PQA-S. The Sheet Numbering System, an option with PQA-S, prints a unique number on each sheet to facilitate identification of problems and guarantee traceability. Because repeat jobs are very common in the packaging industry, a function allows settings used in the past to be quickly searched and set. This improves operability and shortens makeready time. A new color correction function that enables accurate feedback of special colors by the use of L*a*b* values has been developed and incorporated in PDC-SX. In addition, a new function of the Lithrone GX40 automatically positions the image on the sheet in the correct position for the die-cutting process. These functions provide greater print quality stability and higher productivity.
A new system that accurately recognizes die-cutting data and facilitates quality control by blanks has been developed and may be specified with PQA-S. In addition, PQA-S masking software that automatically creates the inspection area in advance from the die-cutting data is available. This further strengthens print quality control for packaging.
To attain the utmost in productivity, the automatic nonstop feeder and delivery are available to enable pile changing without operator assistance. These can be linked to a logistics system that transports stock smoothly through the printing plant. Resupply of the feeder and removal of printed sheets are automatically controlled so that the flow of paper to the press is uninterrupted and high-speed printing continues until the end of the run. Ultimate throughput.
The Lithrone GX40RP/44RP: one-pass everything
The seven-color 5-over-2 Lithrone GX40RP+C UV Extended Delivery in cardboard specification shown below can incorporate every automation system, technology and option available for the Lithrone GX40 in a unique configuration that enables double-sided printing without sheet reversal. This design allows single-edge gripping, which makes the margin on the tail edge of the sheets — an unavoidable structural requirement with perfectors — completely unnecessary, so paper costs can be cut by minimizing the sheet size. Eliminating sheet reversal ensures stable sheet transport that is capable of handling either light or heavy stocks through the use of four double-size transfer cylinders. Front/back plate imaging is in the same direction, just as with single-sided presses, increasing efficiency in prepress.
This machine addresses a growing need in package printing, particularly with cosmetics and other beauty products — double-sided printing. The Lithrone GX40RP's single-side gripper margin not only saves on paper and board costs, this design is perfect for heavy stock due to the simple sheet transport structure. And now Komori has just announced the new Lithrone GX44RP, further widening the prospects for one-pass double-sided package printing.
Available with A-APC Asynchronous Automatic Plate Changer, PDC-SX Spectral Print Density Control-SX Model with the PDF Comparator System, and the PQA-S Print Quality Assessment System for Sheetfed in either single or dual camera specification for the highest levels of quality and productivity in the industry. The Lithrone GX40RP delivers an indomitable competitive edge. Lightning-quick job changeovers with the power of KHS-AI, A-APC and Smart Sequence. Truly a press like no other.
The seven-color 5-over-2 Lithrone GX40RP+C UV Extended Delivery
Robust hardware/software support
Komori Lithrones specified for packaging benefit from an environment of support, compatible hardware and software, and service that works as a printing force multiplier. The Impremia IS29 29-inch Sheetfed UV Inkjet Digital Printing System is the ideal digital solution for high-quality prototyping and testing, offering an expanded color gamut and printing on any stock without coating.
Connecting users and Komori, KP-Connect is software that improves productivity by enabling instant visualization of press operating conditions on the cloud, anytime and anywhere. This means Komori will be able to propose ways of improving printing operations to achieve greater throughput. This package can be upgraded to KP-Connect Pro Printing Task Control Software, an interface connecting MIS and the press that automates the prepress and postpress workflow.
Postpress lineup fills out
The expanding range of Komori Apressia postpress devices — programmable guillotines and die cutters — are designed to match a Lithrone pressroom perfectly. High performance with robust engineering and possibilities for customization to meet specific applications. In short, Komori packaging solutions are the total answer. Reliability beyond measure. A system-of-systems approach to proven technologies and printing excellence. The shortest path to a competitive edge in print.
There is, however, an even more important reason to choose Komori's state-of-the-art solutions. Komori is committed to providing configurations that can be customized for each user's particular application. Komori puts its design and engineering capabilities behind each individual machine. Komori service is also legendary in the industry. When a customer selects a Komori machine, he's also selecting the ultimate weapon: Komori people.
Cosmetics packaging often requires special coating effects and double-sided printing to optimize shelf appeal and attractiveness in use. This eight-color Lithrone GX40RP plus double coater is the only machine in the world that lays down two colors on the back, prints two colors on the front, dries, prints four more colors, and then applies two kinds of coating - all in one pass without reversing the sheets. Specified for special substrates to minimize static and scratching risk. Incorporating the mainstay Komori quality control systems, PDC-SX and the PDF Comparator, as well as the nonstop production system. Configured to provide maximum flexibility and to meet the requirements of diverse applications.
Pharmaceutical packaging in every country is subject to stringent rules for consumer protection. This six-color Lithrone GX40 plus coater and extended delivery is specified to facilitate quick color changes, extreme quality control and reliable inspection. To ensure perfect quality, the machine is specified with PDC-SX, PDF Comparator and the PQA-S All-in-One Model that provides print quality inspection, color control and automatic register adjustment. The double-pile delivery offers physical separation of production sheets and misprints detected by the inline PQA-S. Also specified with the Inkjet Numbering System, a PQA-S option, for traceability. A paper dust cleaning unit is situated in front of the printing units.
Printing of food packaging regularly involves long runs and, of course, extra attention to quality and hygienic conditions. This six-color Lithrone GX40 plus coater is configured for high-speed nonstop production, with a nonstop feeder and delivery as well as the conveyor-equipped logistics system for round-the-clock operation. High-pile delivery and 900mm plinth height further streamline production. The advanced ink roller cleaning system is run by an automatic control program to save time and reduce presoaked cloth consumption. Full set of quality control systems, including PDC-SX, PDF Comparator and PQA-S V5.