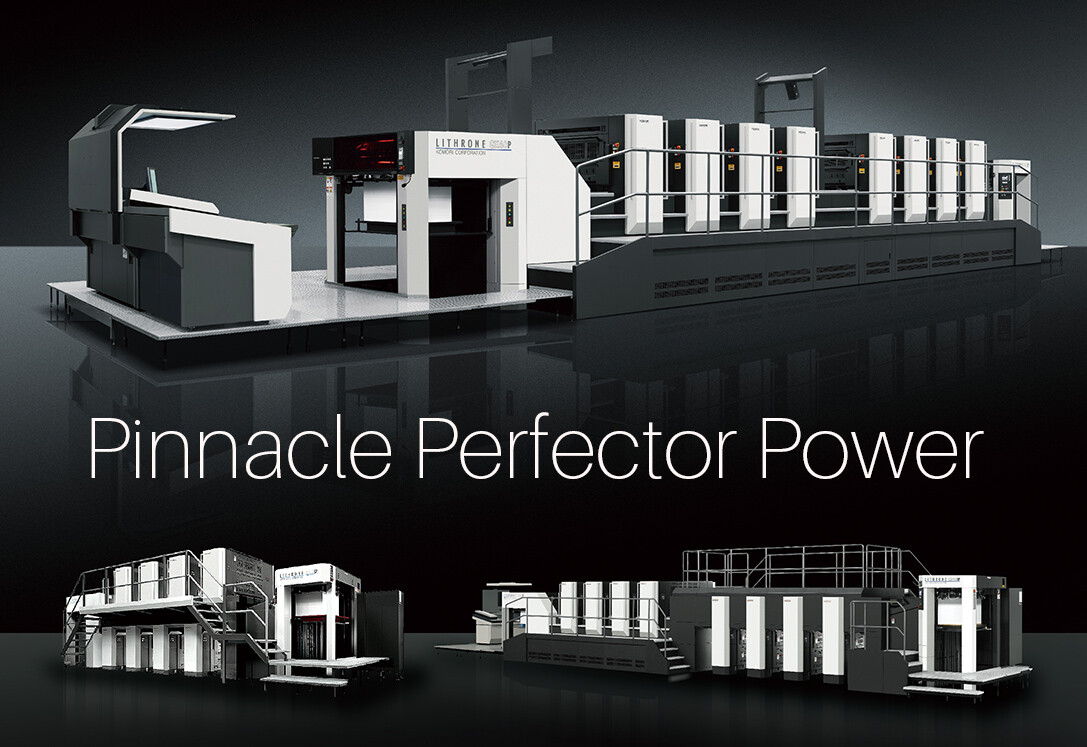
The Lithrone GX40P perfector has joined the Komori lineup of double-sided printing presses. The new press has a maximum printing speed of 18,000 sheets per hour and prints B1-size images. This machine was developed as the latest press incorporating technologies for high-speed, stable operation, such as the independent drive system of the feeder in the flagship Lithrone GX40, and advanced mechatronics technologies, such as the PDC-SX Spectral Print Density Control - SX Model and the PQA-S Print Quality Assessment System (Sheet). These technologies support the operator and ensure high productivity. The current Komori lineup of double-sided presses is represented by three leading models, each with a different mechanism: the Lithrone GX40P, the Lithrone GX40RP and the Lithrone S40SP. Since 2000, Komori has shipped more than 900 double-sided printing presses worldwide. Here we look at the features of these models and what sort of printing they are used for.
New: Lithrone GX40P
New Lithrone GX40P sheet reversal mechanism is simple and rigid for stable operation at 18,000 sph
Equipped with a perfecting cylinder that reverses the sheets, this convertible perfector-type press is capable of not only one-pass double-sided printing but also single-sided multi-color printing. Thus, this highly flexible press provides the productivity of double-sided printing and the added value of multi-color printing.
Komori's unique configuration uses three double-size cylinders, for the impression, transfer and sheet reversal cylinders, reducing bending of the sheets by the cylinders and lessening stress on the sheets as they are transported. This design enables smooth single- and double-sided printing — even with thick sheets.
The Lithrone GX40P differs from the Lithrone G40P in realizing high-speed, stable operation at 18,000 sph in double-sided printing due to the use of a new sheet reversal mechanism that is both simple and very rigid. Also, the parts maintenance load is low and quality stability is such that change in front/back register accuracy due to aging is limited because of this simple construction.
On the Lithrone G40P, when the sheet width is changed, the sheet reversal unit suction points manually adjust sheet size. On the Lithrone GX40P, however, these are linked to the paper size and adjustment is automatic. And Smart Sequence, the automatic print changeover function, not only shortens changeover times but also eliminates operator adjustment errors. The front/back register measurement function of PDC-SX is very well suited to double-sided printing presses. In adjusting the front/back register marks by the conventional method, the operator checks their positions by holding the sheet up to the light. For thick sheets, which cannot be checked by this method, the amount of difference between front and back registration is determined by piercing the center of the register marks with a needle.
These methods are not quantitative. PDC-SX quantitatively measures the amount of difference between front and back register and, by feedback to the press, reduces front/back register checking and adjustment time as well as paper used for adjustment, thus lightening the operator's workload.
In addition, PDC-SX and PQA-S support test printing to production printing by means of in-line quality inspection, color control and automatic registration functions. The automatic OK sheet assessment function, an approach incorporated in Autopilot, automates all processes from test printing to production printing, not only shortening print start-up time but also standardizing test printing processes. The combination of Smart Sequence, Autopilot and one-pass, double-sided printing with the Lithrone GX40P enables standardization and maximizes productivity.
By using high-sensitivity UV (H-UV) or LED UV systems before the perfecting unit and in the delivery, one-pass, double-sided printing with UV coating can be performed with instant curing. Since there is no waiting for drying and the work can be immediately passed to the next process, printing productivity is high and the time for finishing processes is shortened, assuring total productivity improvement.
Paper Saving: Lithrone GX40RP
Although the Lithrone GX40RP double-sided printing press also has a maximum printing speed of 18,000 sheets per hour and prints B1-size images, this press does not have a perfector-type sheet reversal mechanism.
Sheetfed offset presses transport paper by gripping the sheets with grippers. The sheet reversal mechanism of the perfector-type press, however, changes the grip from the leading edge to the tail edge when reversing the sheets, and therefore a gripping margin on both edges of the sheets is necessary.
However, the Lithrone GX40RP enables one-pass double-sided printing by passing the sheets through three double-size transfer cylinders and one suction drum (RP unit) when changing from back-side to front-side printing.
In other words, since changing gripping from the leading edge to the tail edge is unnecessary, there is no front/back register gap when changing grippers and paper cost can be reduced because there is no tail-edge margin.
Although paper sizes vary worldwide, the regular sizes for printing stock in Japan are 625 x 880 mm and 636 x 939 mm. When printing an 8-up A4-sized image on one side or 16-up on both sides, a perfector-type double-sided printing press must use 636 x 939 mm paper since a tail-edge gripper margin is necessary. However, since the RP-type double-sided printing press does not need a tail-edge gripper margin, it can print on 625 x 880 mm stock, thus saving on paper costs.
In addition, since the Lithrone GX40RP has no complex sheet reversal mechanism and provides simple sheet transport with single-edge gripping, it can print on thicker paper than the Lithrone GX40P. The perfector-type press can print paper up to 0.6 mm in thickness, while the RP-type press offers the advantage of being able to print on paper up to 0.8 mm in thickness.
More and more printers are implementing one-pass double-sided printing with special colors on the back side and added value printing on the front side using the RP-type package specification press with one or two colors on the back side, six or seven colors on the front side and a coater.
The Lithrone GX40RP, however, is structurally unable to perform the multi-color printing that the Lithrone GX40P is capable of. It is a dedicated one-pass double-sided printing press.
While not able to perform one-sided multi-color printing, the Lithrone GX40RP is the press for high-speed one-pass double-sided printing with lower paper costs. For high speed and the flexibility of both one-sided multi-color and one-pass double-sided printing, the Lithrone GX40P is the answer. Users in Japan and Asia are tending to choose the RP type, while those in Europe and North and South America are favoring the perfector type.
Space Saving: Lithrone S40SP
The cylinder array of the Lithrone S40SP, released in 2005, is a unique structure that prints the front and back sides alternately and uses no transfer cylinders. The advantage of this structure is that it allows installation of a four-color double-sided press in almost the same space as a 40-inch four-color single-sided press. Particularly where factory buildings are small, as in Japan, the Lithrone S40SP is an extremely good match for sites that will not accommodate a Lithrone GX40P or a Lithrone GX40RP double-sided press. Although the Lithrone S40SP cannot perform single-sided multi-color printing because it uses a single-edge sheet transport system like the Lithrone GX40RP, many single-color, two-color and four-color double-sided machines capable of printing books, catalogs and textbooks have been installed in Japan and China.
In the unique cylinder array that prints the front and back sides alternately, a special ceramic jacket on the surface of the alternately arranged front- and back-side impression cylinders is necessary to prevent the adhesion of conventional ink on wet sheets to the surface of the next impression cylinder. While this may seem to suggest UV printing, such an option would require installing a UV lamp on each printing unit since the front and back sides are printed alternately, an impracticality from the viewpoint of UV lamp installation cost and running cost.
Since the front- and back-side impression cylinders are arranged alternately in this array, this press is able to print paper up to 0.2 mm in thickness due to the gap between the cylinders. Therefore, the Lithrone S40SP is utilized as a dedicated double-sided press in commercial printing using conventional ink, holding down installation space requirements and running costs.
Since 2010, UV has increasingly spread into commercial printing with the release of high-sensitivity UV ink, and there are more and more installations of perfector-type and RP-type double-sided presses capable of not only conventional printing but also UV printing. In recent years, the adoption of LED UV systems has increased in line with the desire to save energy.
Komori provides three types of outstanding double-sided printing presses to raise customers' productivity and cost performance.
Lineup of double-sided presses
-
Total shipments of full-size double-sided presses From 20 presses in 2000 to more than 900 by 2019 Note: In the printed version, the P and RP sections of this graph are reversed. This PDF is correct.