Connected Automation: Komori's IoT-based Solution for Maximum Productivity / Part 2
Lithrone GX40RP/G40 advance DEMOs & VOICEs
20 January 2021
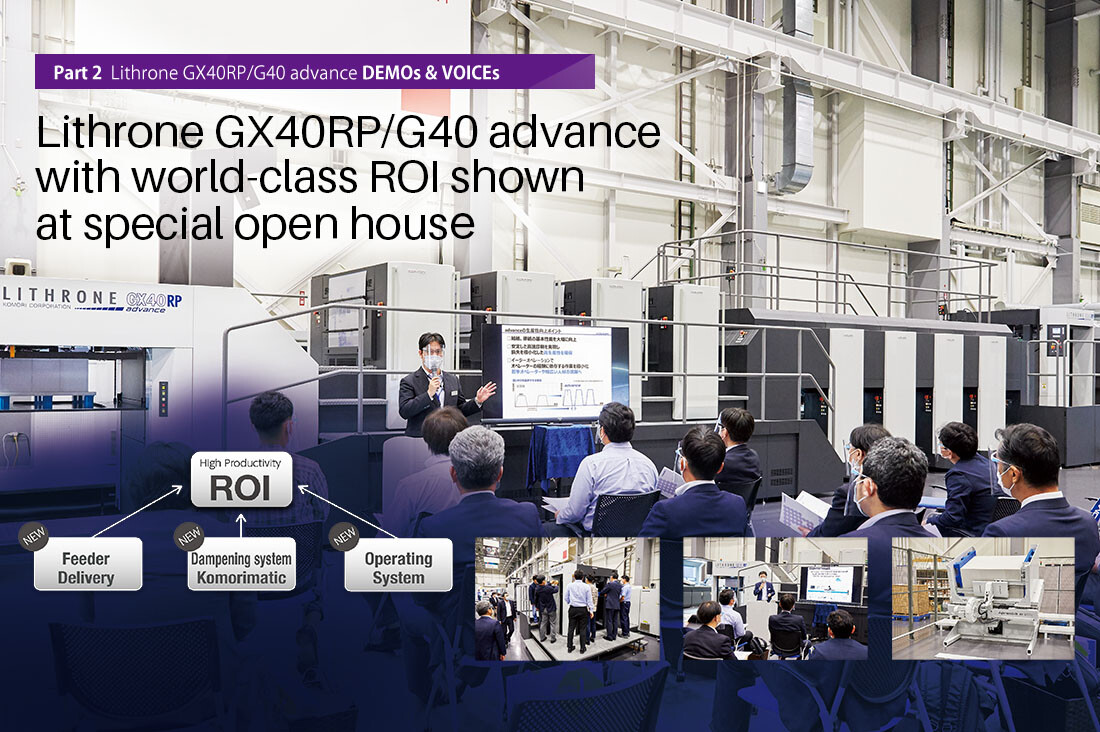
The demonstration introduced press automation featuring touchless printing from Job 1 print start-up to the end of Job 2 using Parallel Makeready and Autopilot
With the Lithrone GX40RP advance, visitors saw a demonstration of Autopilot automatically performing two jobs of one-pass, double-sided printing at 18,000 sph from touchless print start-up and job changeover to the end of the run. The real experience of Komori's Connected Automation concept. Using the scheduler with high-level job data linked from KP-Connect Pro, the operator performed automatic press operation with just one job start button. By means of Parallel Makeready, this automatic operation realizes minimization of changeover time, quick acquisition of color, automatic register adjustment and the quality OK determination, all by a printing system developed in-house by Komori.
Visitors to the Komori Graphic Technology Center were able to see first-hand the color adjustment and register control in high-speed printing on the newest operation stand, the PQC-S V6-equipped KID Komori Information Display.
Based on high productivity and fast job changeover, these printing solutions can contribute to solving the issues of labor shortages and losses that customers always face in commercial printing.
Participants were interested in the stability of the feeder/delivery and the accuracy of color control.
Smart Color wide-gamut printing system using multicolor process colors
Demonstration 2 showed package printing on cardboard with the Lithrone G40 advance by means of Smart Color technology being developed by Komori. Smart Color is a technology that minimizes production losses due to color changeover tasks, the biggest issue facing package printing users, already weighed down by inventory management of special inks and the trend toward high-mix, small-lot production. The inks are fixed to six process colors (seven colors), and basic color reproduction of dots is performed to simulate approximately 80% of Pantone colors (85% in the case of seven colors).
According to a Komori survey, the average job changeover time (including color change) for Japanese package printers is about 45 minutes, and the number of test prints is about four, which creates significant loss of production.
In the demonstration, actual samples were used to show how color reproduction matches that of printed materials with six-color Smart Color separation, in contrast to conventional solid spot color printing. Technology that minimizes start-up paper waste by quickly acquiring color and register with KP-Connect Pro and Komori's renowned printing systems was also introduced.
In addition, the demonstration highlighted on an actual press the advancements made to the feeder, delivery and the Komorimatic dampening system, which ensures high-level color reproduction through sharp dot reproduction and offers technology to minimize color variation on printed sheets. Moreover, visitors experienced the benefits of Komori's high basic performance and latest systems, including fast color okays and automatic control of register by KP-Connect Pro's press automation, printing at the maximum operating speed, and the assurance of high print quality from start-up to high-speed production printing. During the demonstration, test printing and production printing samples were measured using a spectrophotometer showing the color difference between the spot colors and each of the pseudo spot colors. The visitors could confirm that the results were ⊿E0.5 to 2.0 (or less), with unevenness accuracy of about ⊿E1 in the three-color gray section. With these results, we believe that Komori's solutions based on the Komori advance press lineup will provide high productivity and increased profitability for packaging printers.
Printed samples with solids using special color inks (left) and pseudo-reproduction with Smart Color (right)
Connected Automation is Komori's commitment to promote automation throughout the production process
At this special open house, Komori demonstrated the Lithrone GX40RP/G40 advance printing presses to show how Connected Automation can minimize work that depends on operator skills and maximize production efficiency.
At Komori, we are working hard to meet the ever-changing demands of the print marketplace so that our customers remain efficient and profitable.
PDC-SX spectral print density control shows density changes.
Demonstrations of the Apressia CTX, MB and AT postpress machines were also carried out.
A demonstration of the Impremia IS29 digital printing machine was also presented.
Click below to read Part 1.